Computational Wood Project,
HCI Research
Incorporating sensing and communicating abilities into daily used objects and furniture in a battery-free way where the interaction powers the communication and the objects are made with sustainable wood materials.
With Scott Hudson and Sai Swaminathan
Summer 2022
Fusion 360, Rapid Prototyping, Ubiquitous Computing, 3D Modelling and Fabrication, Design Research
My role as a designer is to consider the interaction one would have with these objects, the form they would take in physical space, their inner workings and mechanisms, their integration with the electrical components, and their materiality.
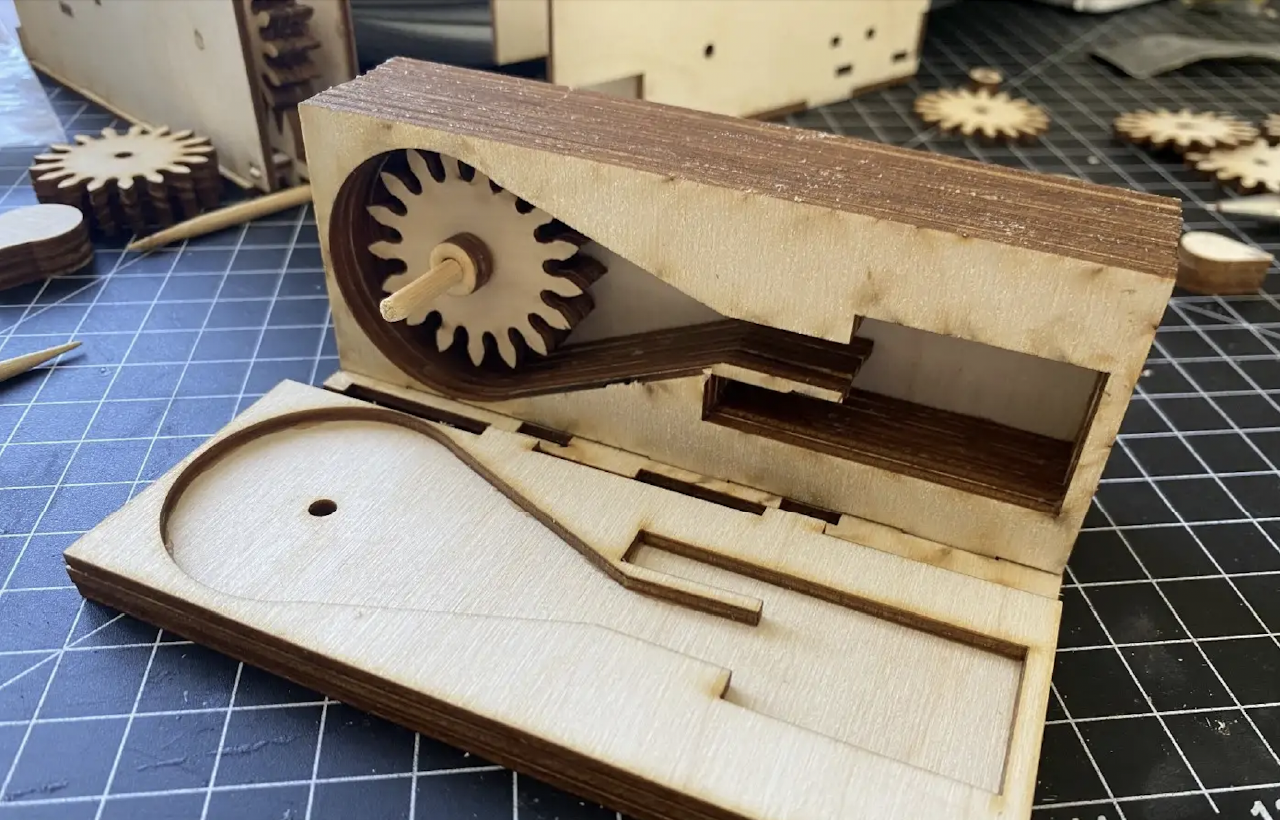
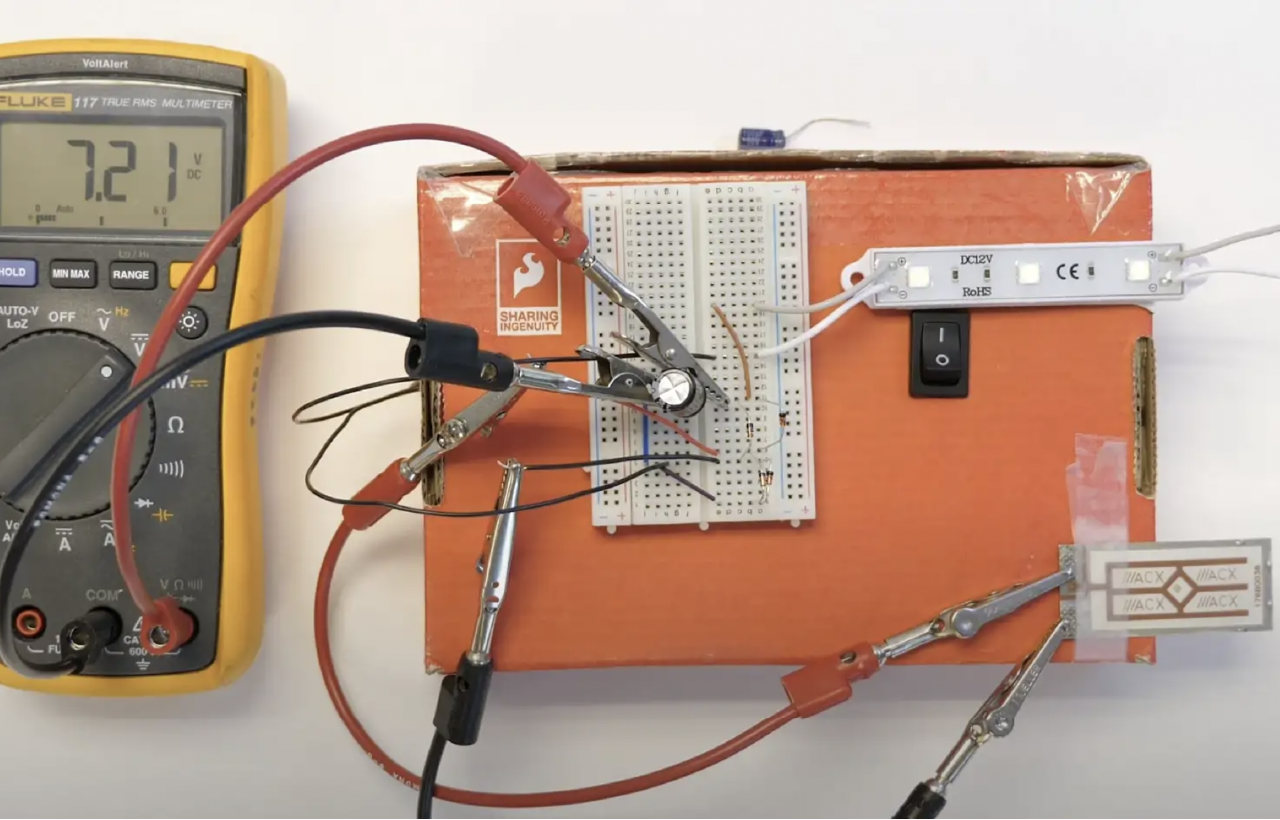

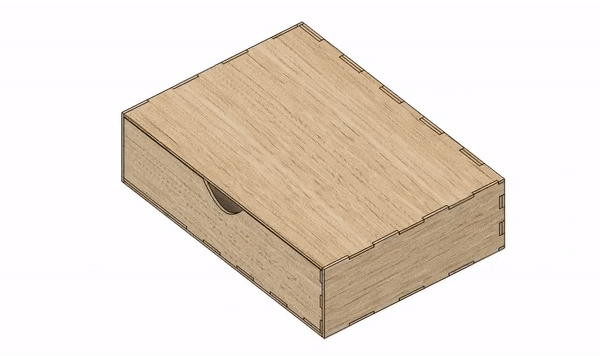
The Drawer
Exploring an object that a majority of the world uses in some manner, and thinking about how we can use it’s mechanical pulling force to our advantage.
The drawer is embedded with the pzt strip and circuit, and it is the motion of pulling open the drawer that flexes the strip and triggers the communcation. The linear motion of the pull converts into rotational motion of the gear.
Exploring an object that a majority of the world uses in some manner, and thinking about how we can use it’s mechanical pulling force to our advantage.
The drawer is embedded with the pzt strip and circuit, and it is the motion of pulling open the drawer that flexes the strip and triggers the communcation. The linear motion of the pull converts into rotational motion of the gear.
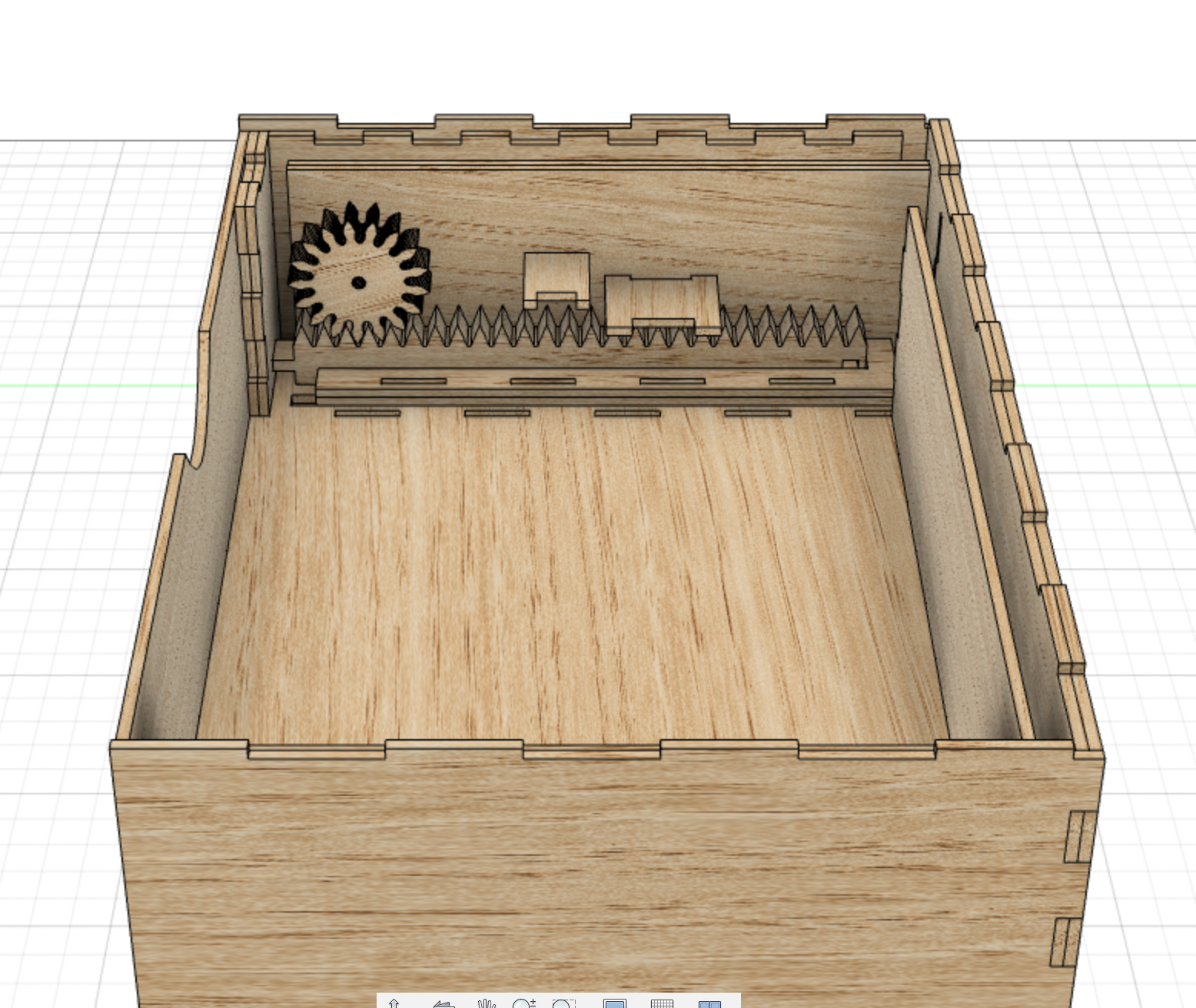
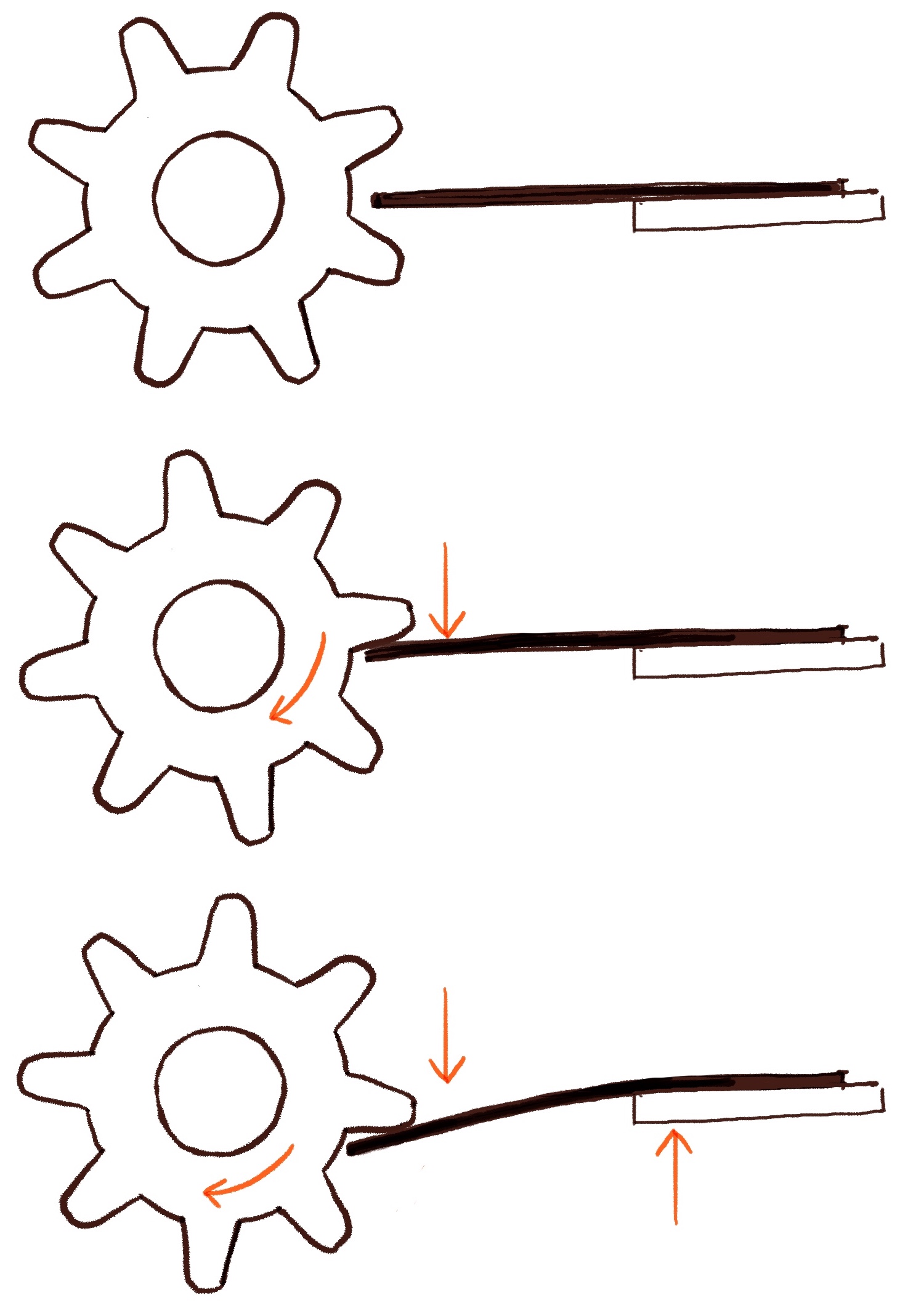
Giving careful consideration to the placement and packaging of the electrical components, and creating a system of mechanical parts that worked effectively without hindering the use of the storage space.
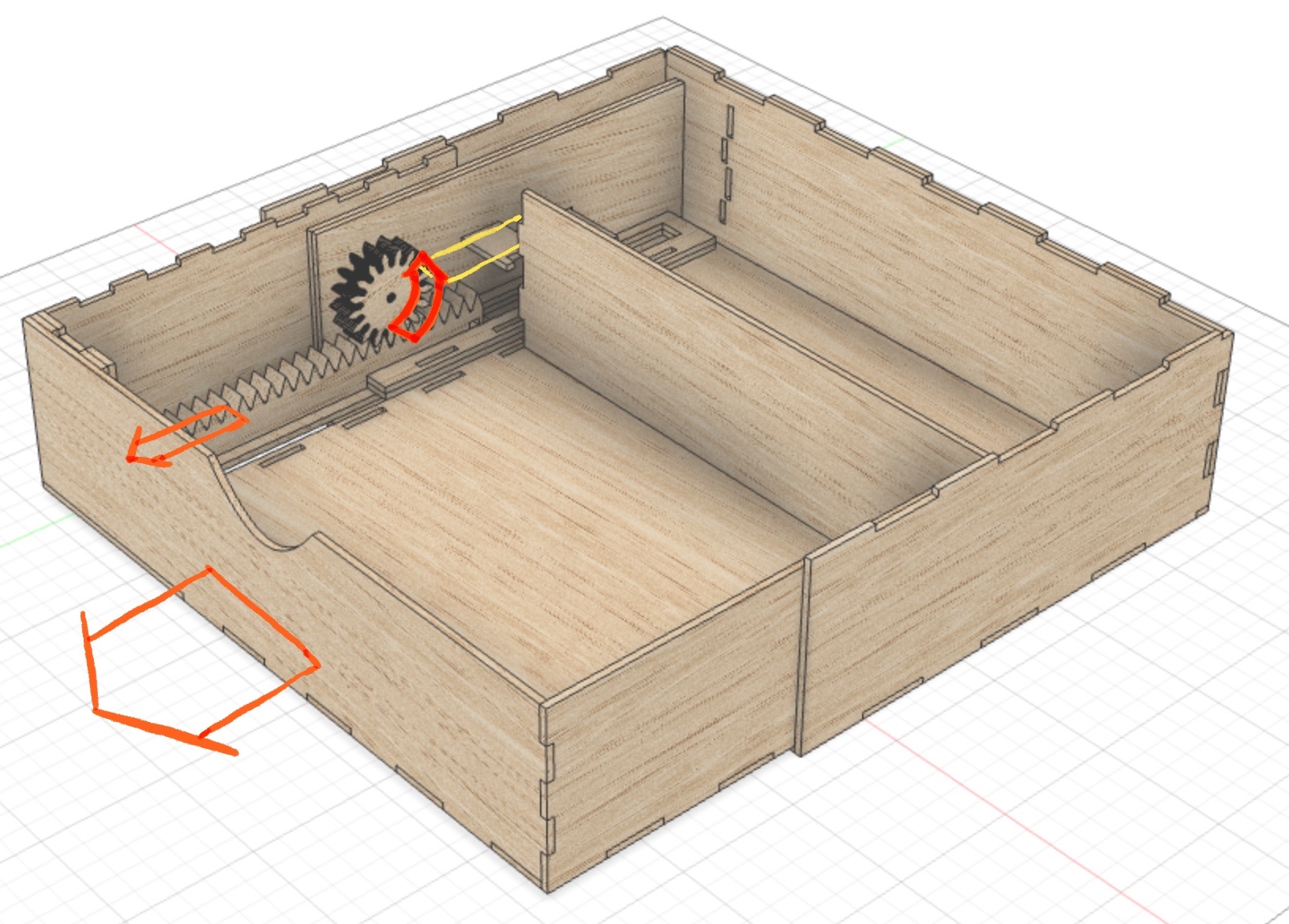
Designing for the gear to stay back within the main housing of the drawer, but the rack to move with the drawer as opened was the main challenege here.
The gear is sandwiched between 2 panels, and spins on a dowel that passes through these walls. These walls are attatched to the back of the drawer housing box, while the rack is attatched to the front of the drawer, allowing for the gear and rack to efficiently interact with each other as the drawer is pulled.
The gear is sandwiched between 2 panels, and spins on a dowel that passes through these walls. These walls are attatched to the back of the drawer housing box, while the rack is attatched to the front of the drawer, allowing for the gear and rack to efficiently interact with each other as the drawer is pulled.
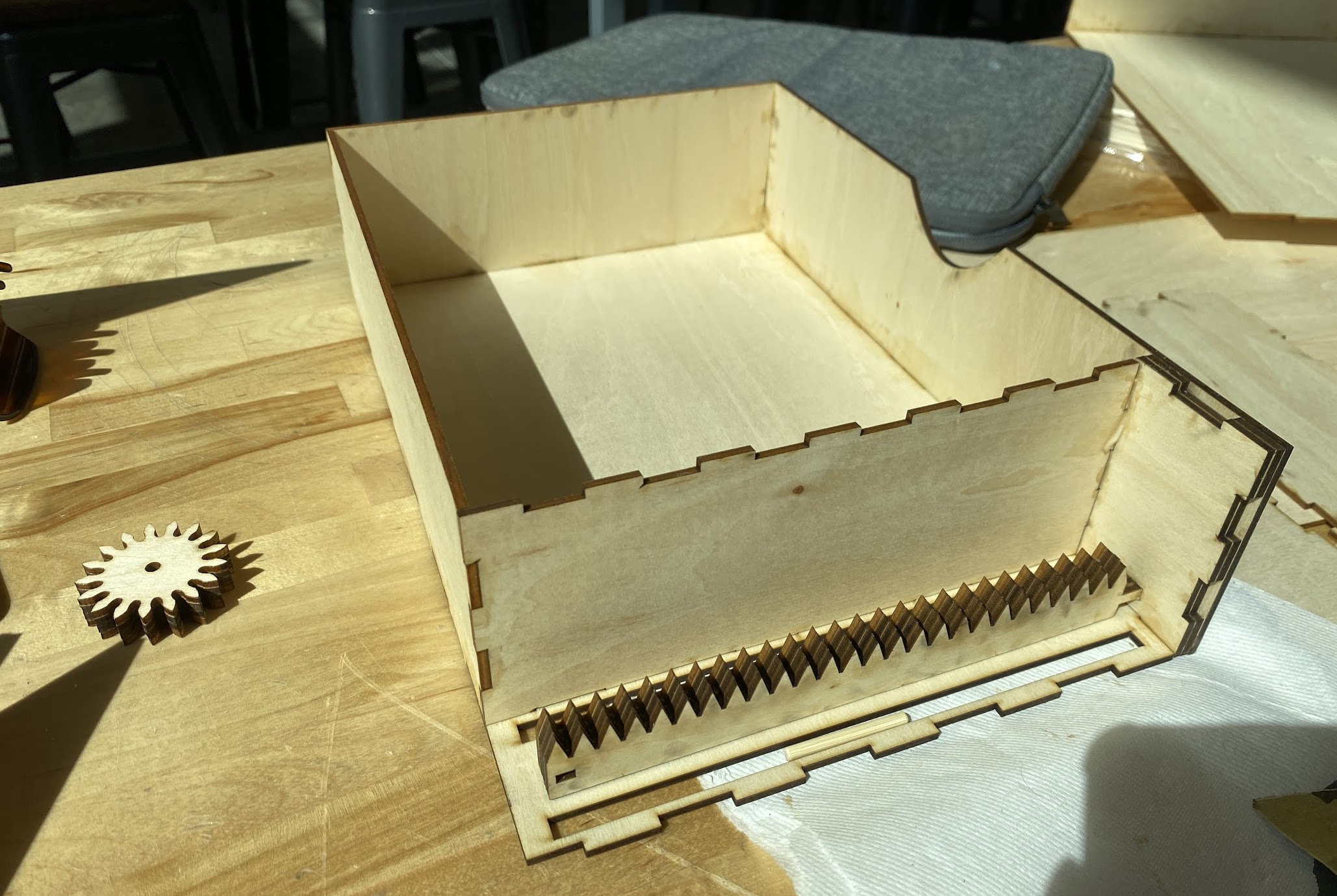
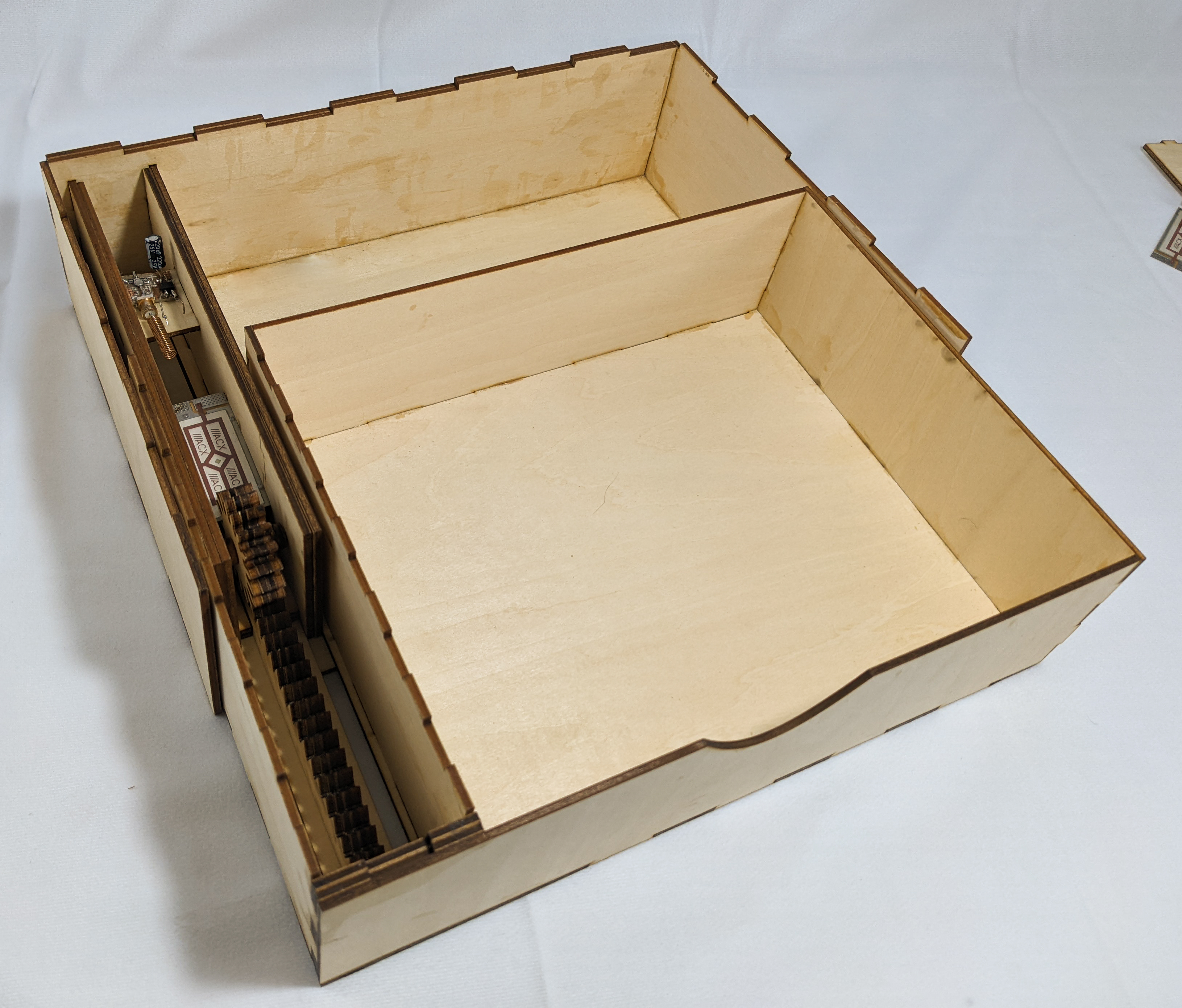

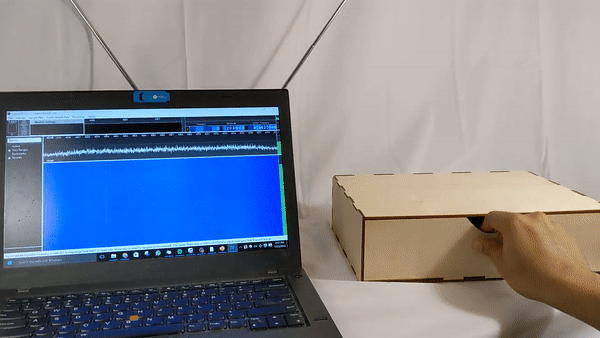

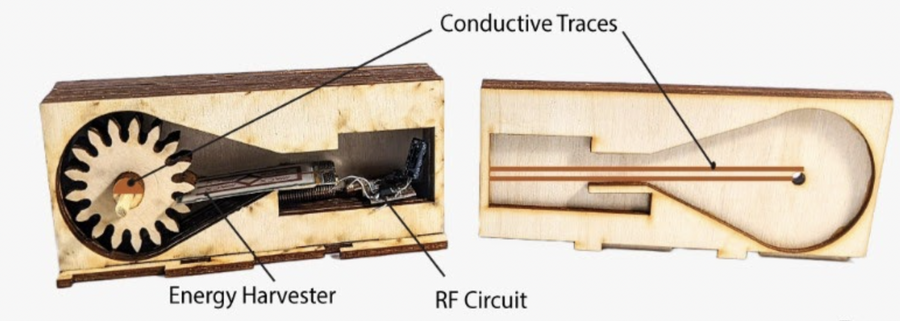
Wooden block unit
Consisting of 1 or 2 control knobs to send signals as necessary, this unit creates the core of our project— a module, built with wood, embedded with ultra low power sensing and communication abilites.
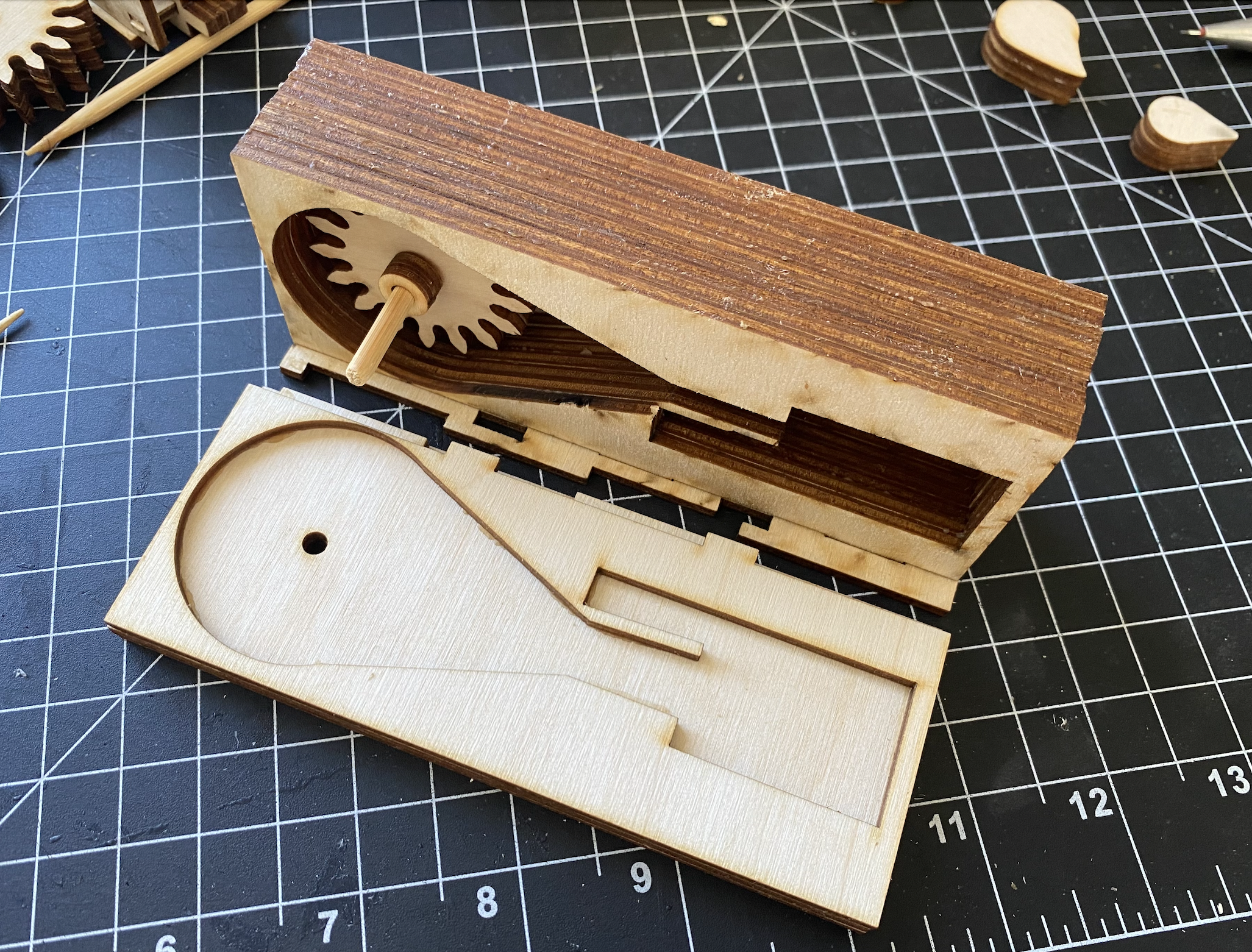
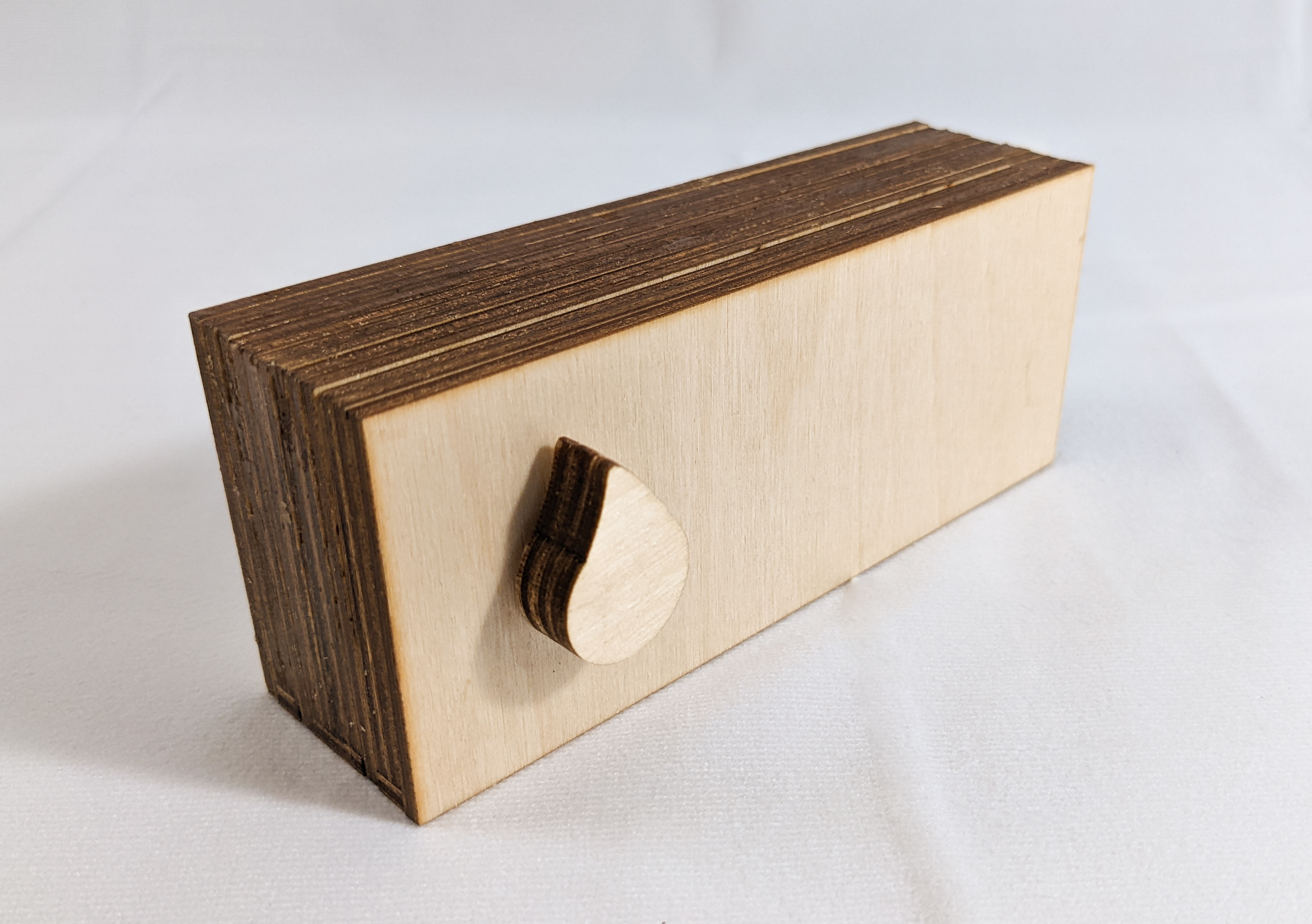
There would be many possibilites for the manufacturing of this unit. Due to resources, we laser cut and laminated sheets of plywood. Alternating the direction of grain for each lamination in this process would create an even stronger material. Alternatively,
the space for embedding the mechanisms could be carved out using shop tools such as the CNC.
the space for embedding the mechanisms could be carved out using shop tools such as the CNC.

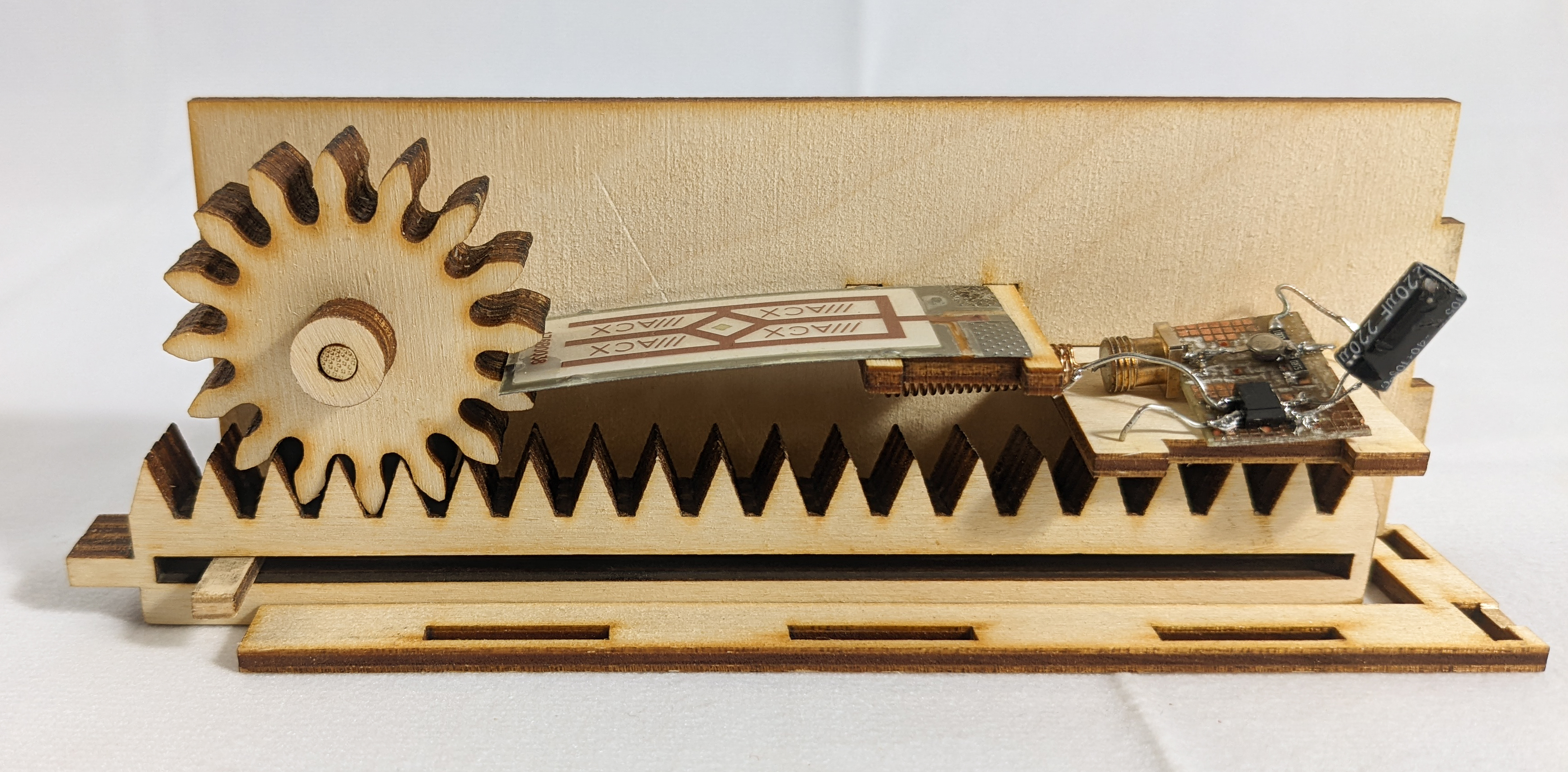
The blocks could be programed to complete a variety of functions—adjusting the volume of speakers, turning appliances like the tv/ lights on/ off.
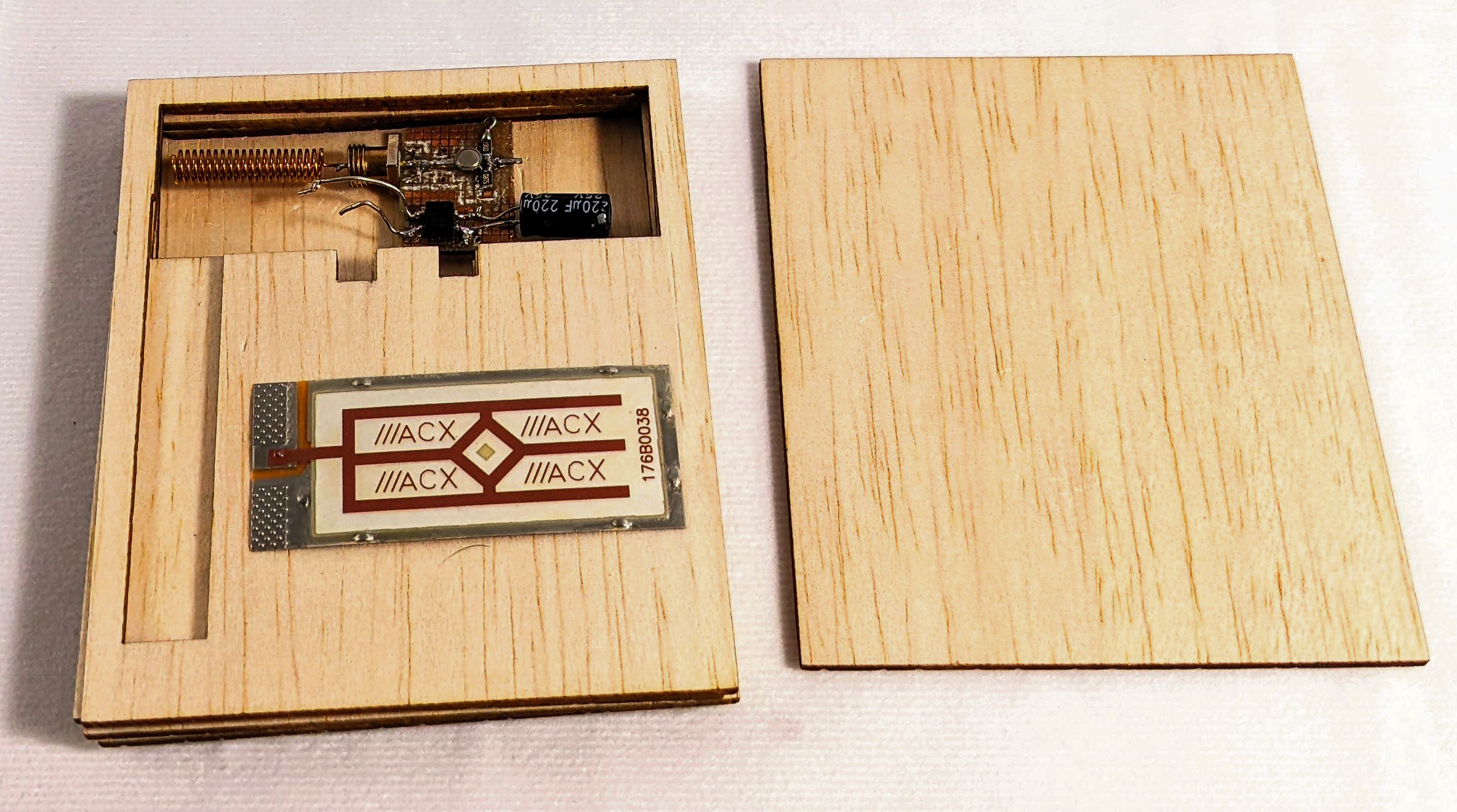
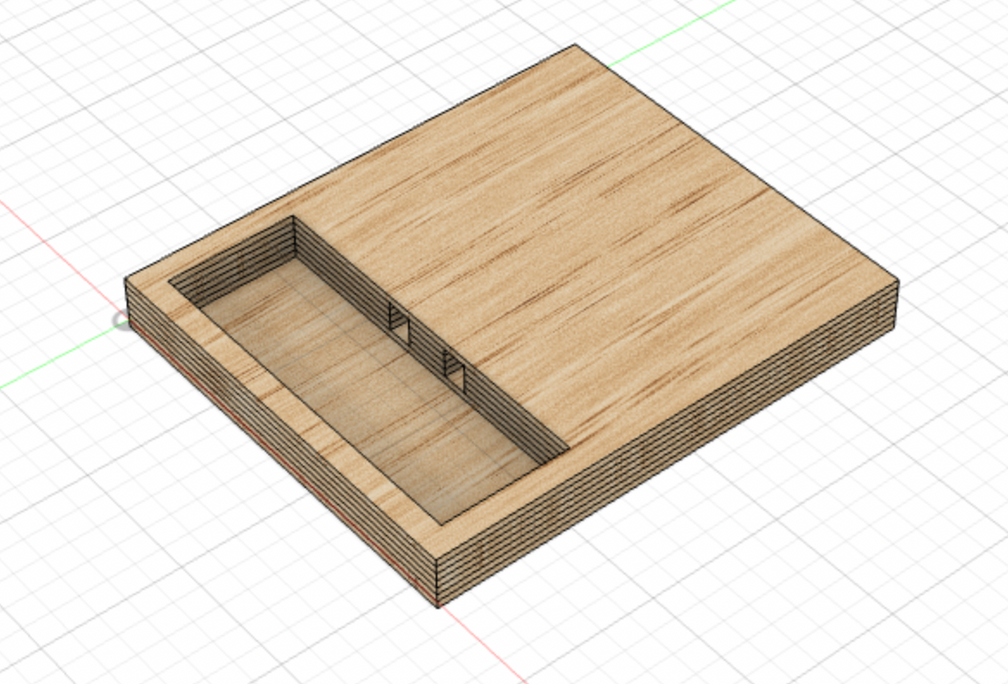

Communicating tile
One application of this research is presented through a thin slice module of wood embedded with the pzt strip and a small circuit sandwiched between flexible wood. We used balsa that allowed a step/ push on the wood to flex the electrical switch and communicate power.
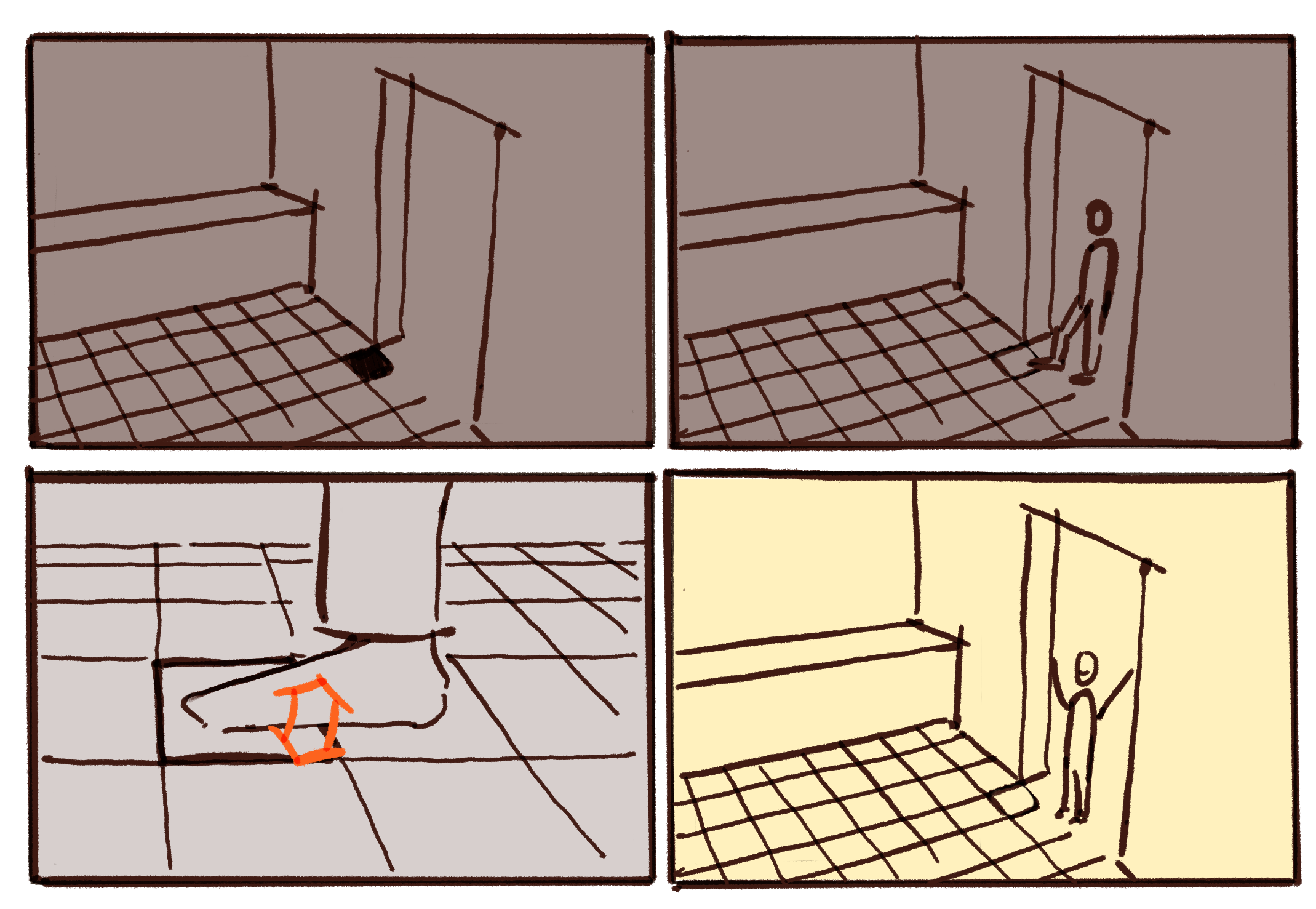

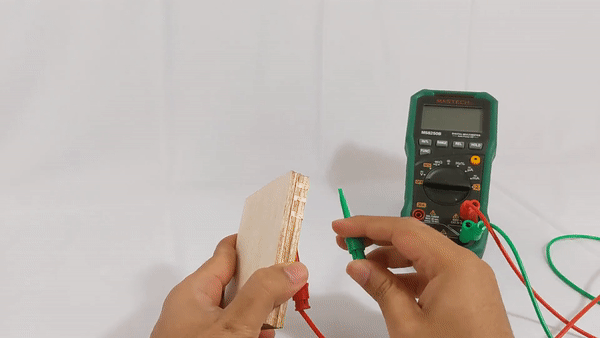

Door handle
The door handle was developed with the same mechanisms as the wooden block unit— it is a direct application. With just a few changes to the interaction. Switching out the knob attatchments to the door handle, and creating the door lock component that is attatched on the same dowel holding the gear, the computational wood is able to detect the opening and closing of doors and communicate the interaction in an effective, battery-free, wireless manner.
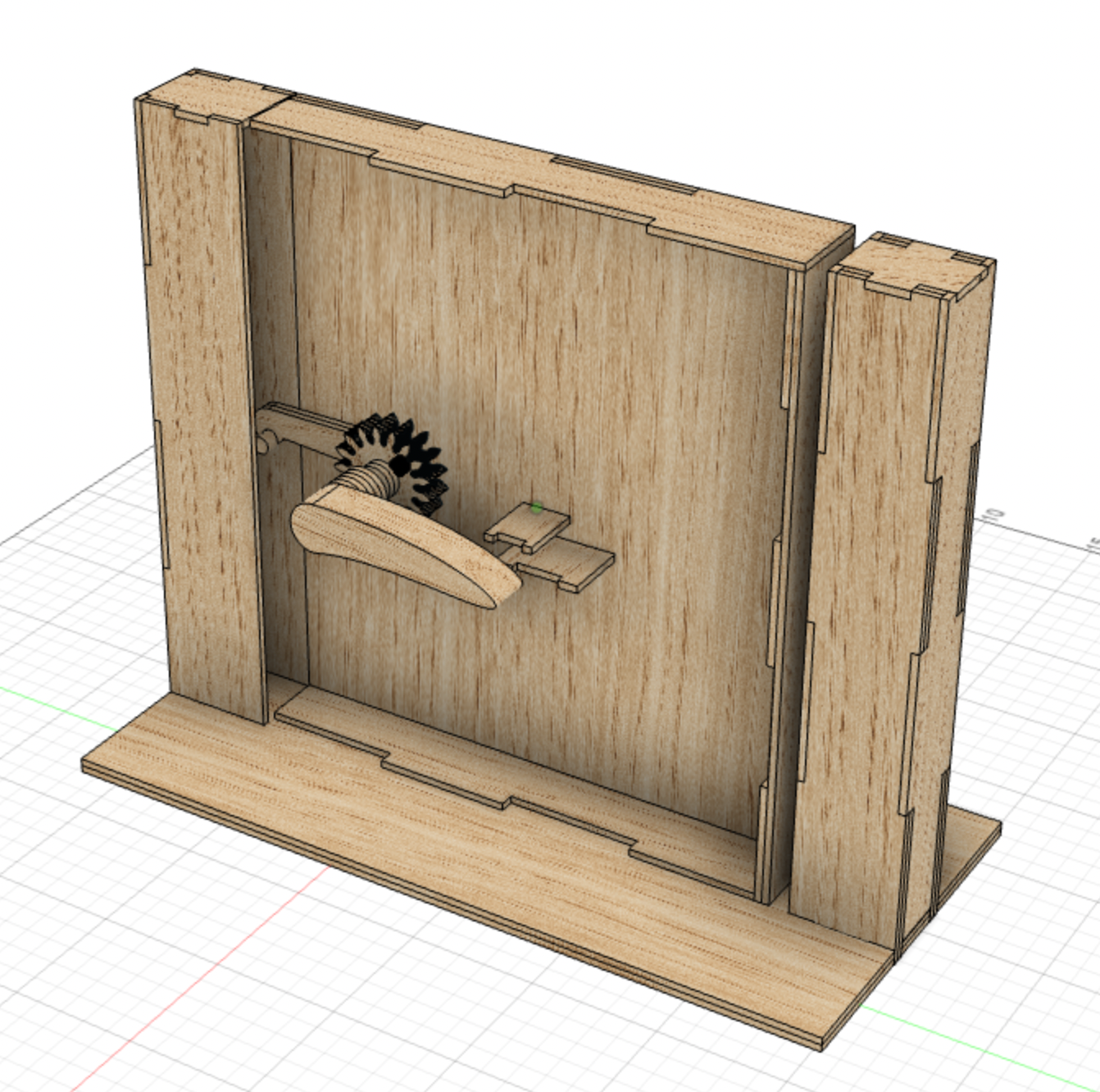
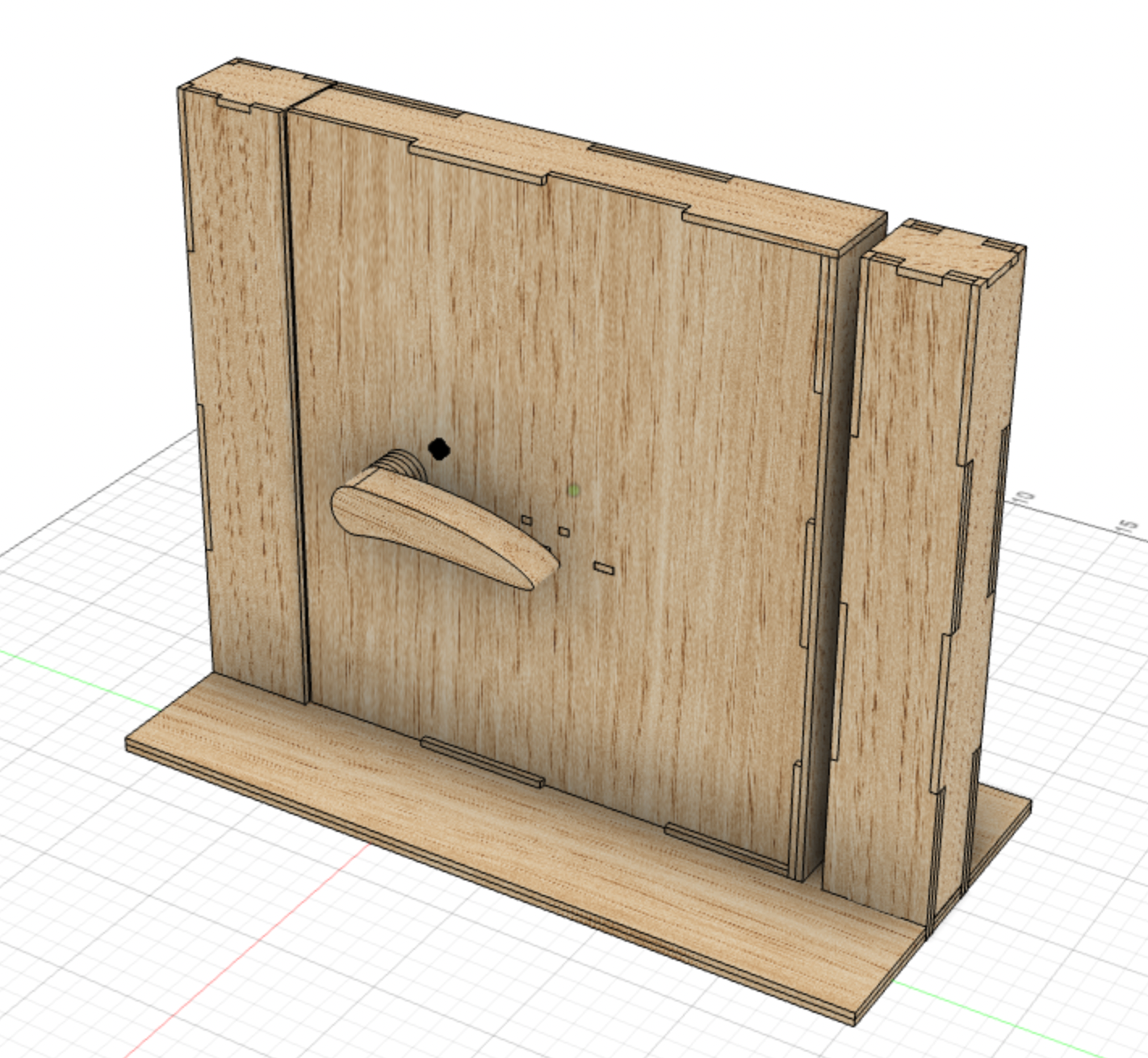
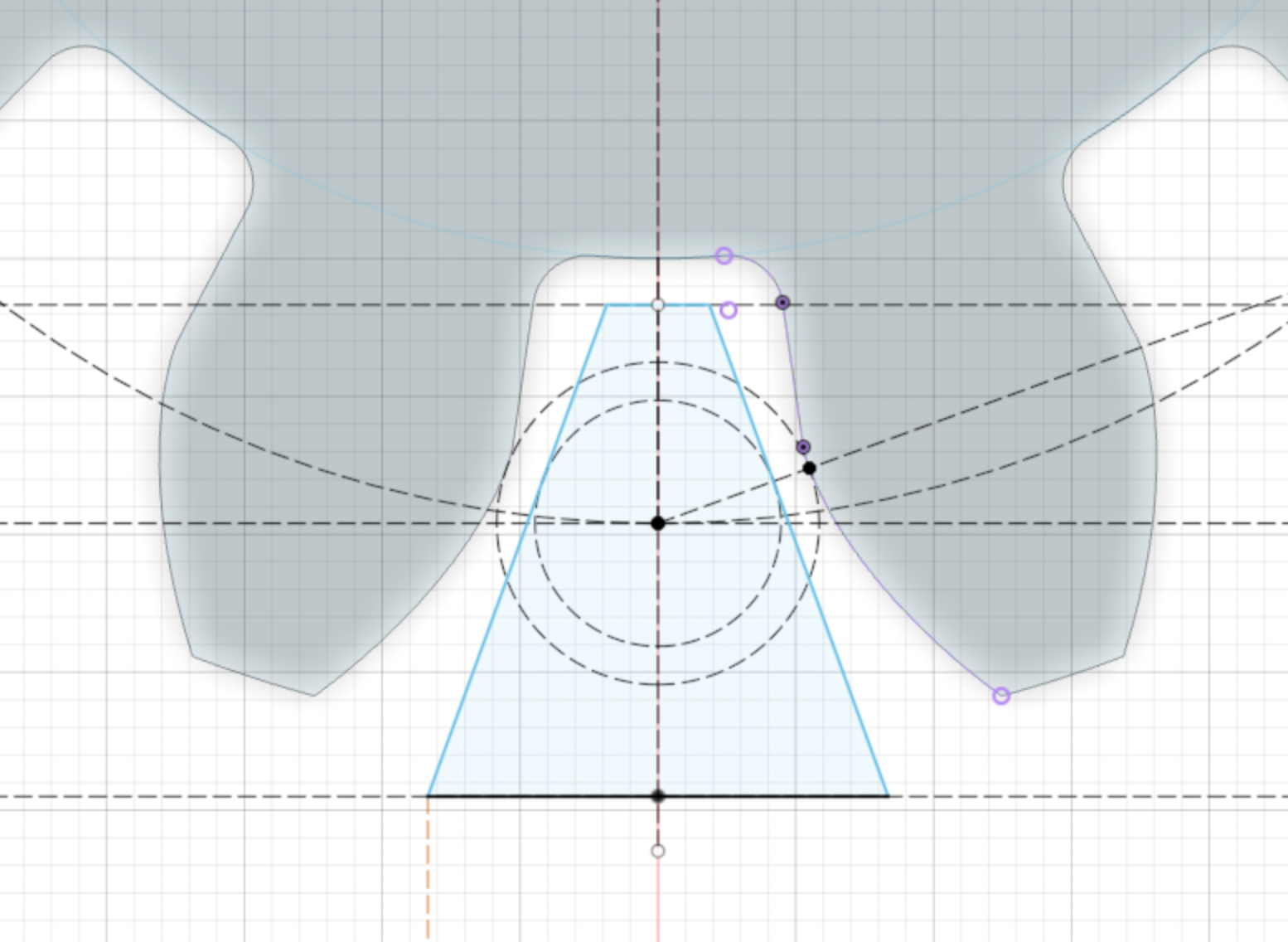
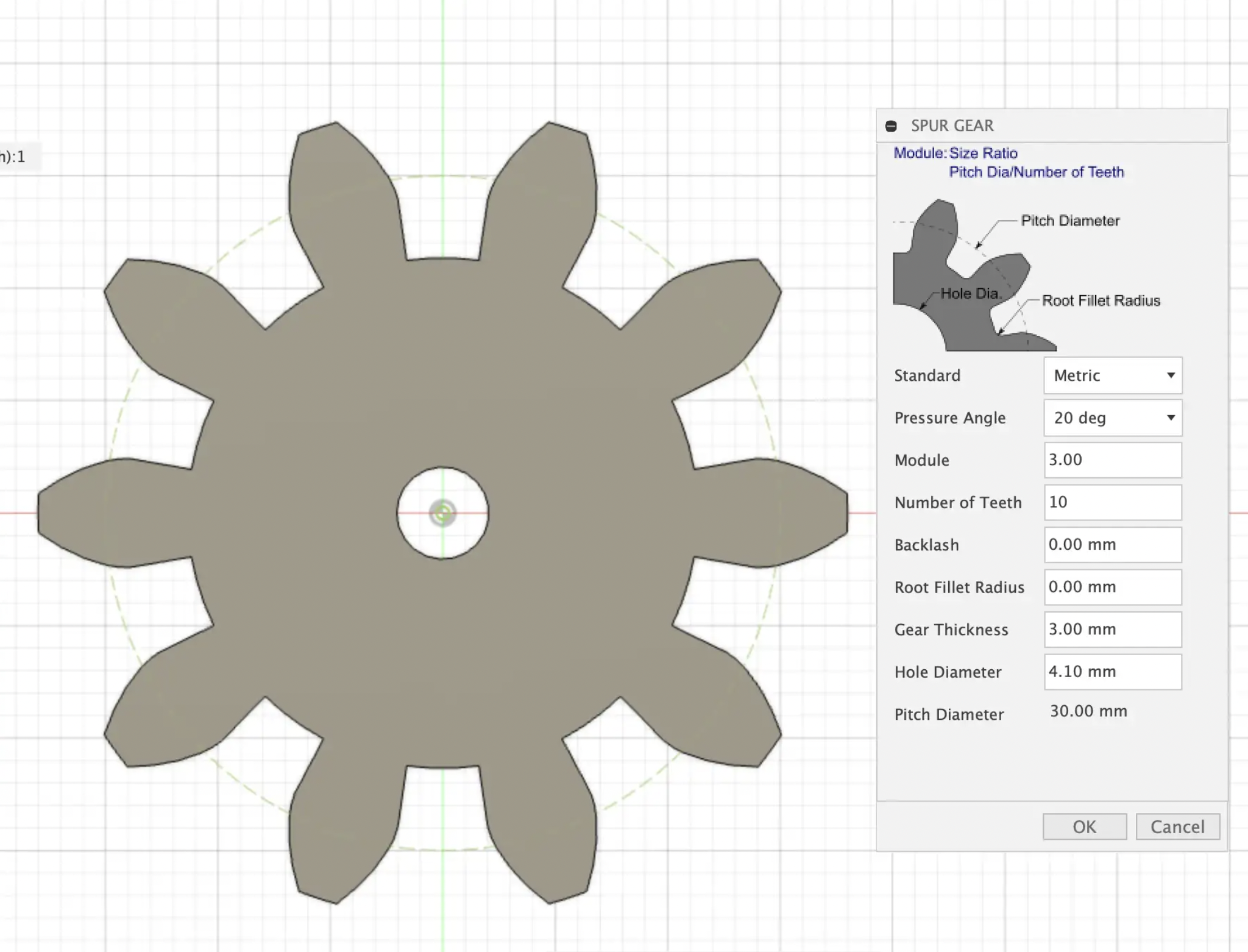
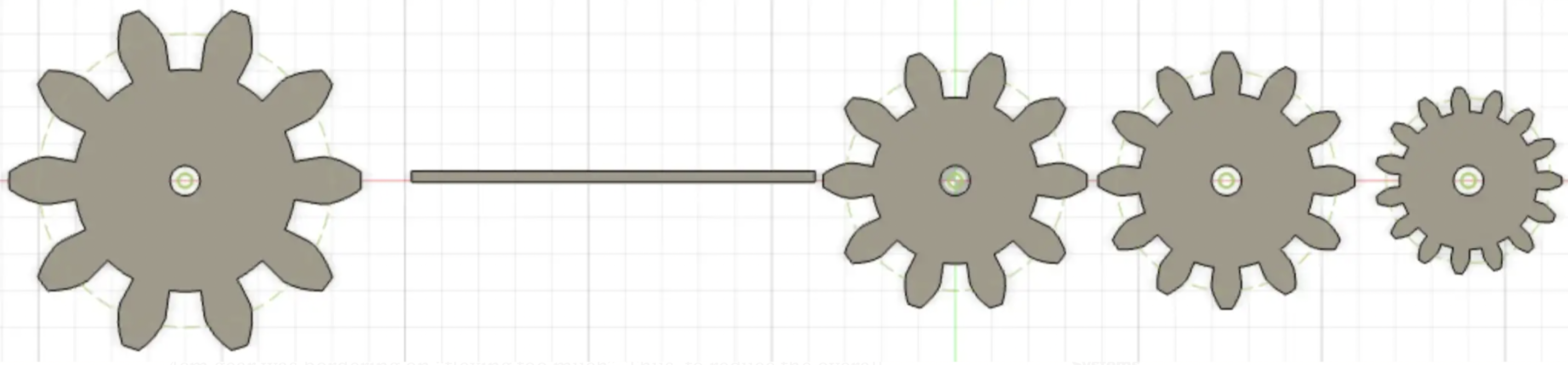
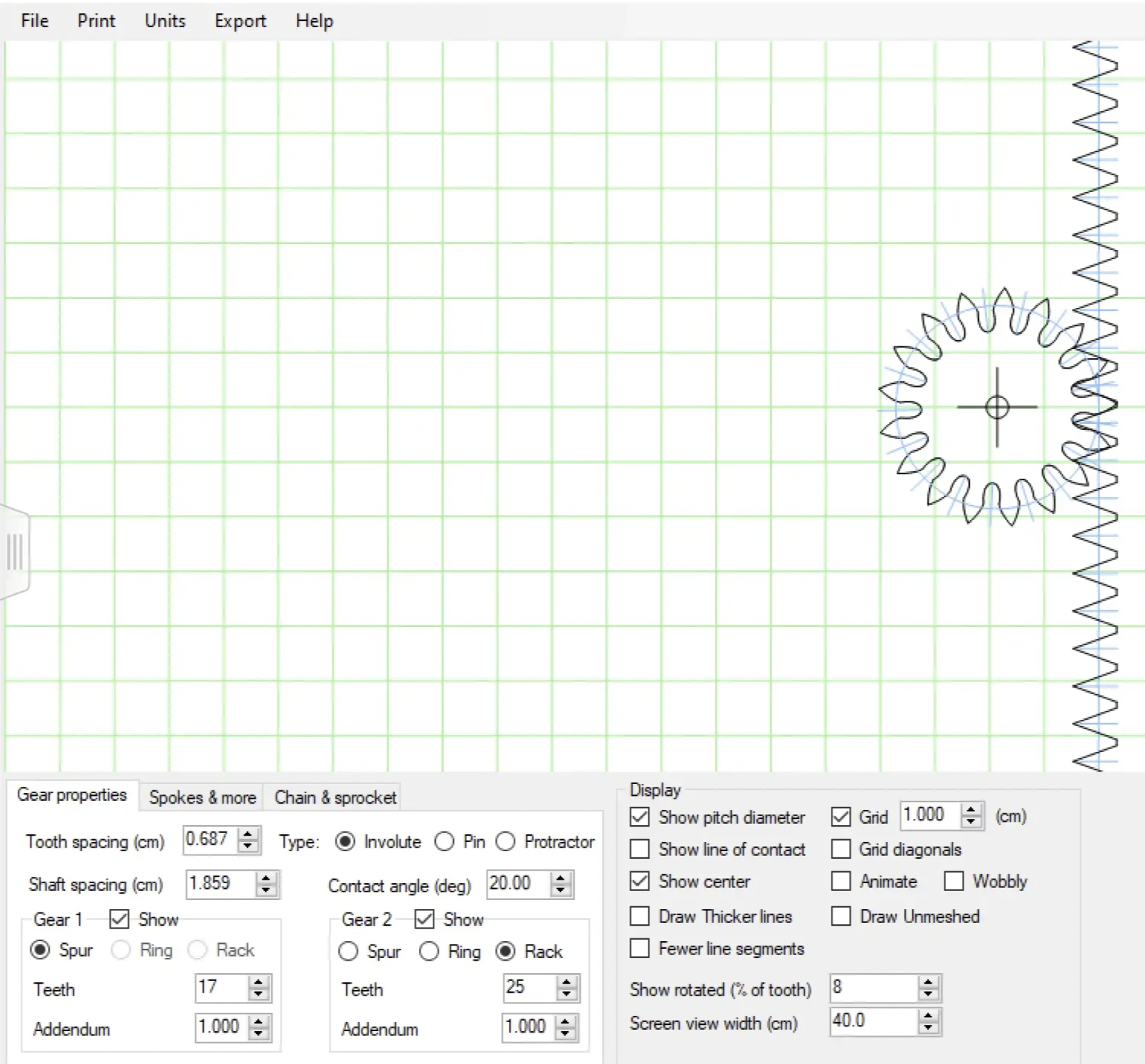
Diving deep into gears
Part of my exploration to create effective mechanisms for our project involved really understanding the geometry and workings of a gear. I learnt and played around with the number of teeth, root fillet radius and distance between the tip and base of the teeth.
Using a special software not included in the 3D modeling program I was using, allowed me to create our ideal gear— one where the teeth are sharp with a large space between the tip and base for the electric strip to slip into— small and compact with a lot of between- teeth space.