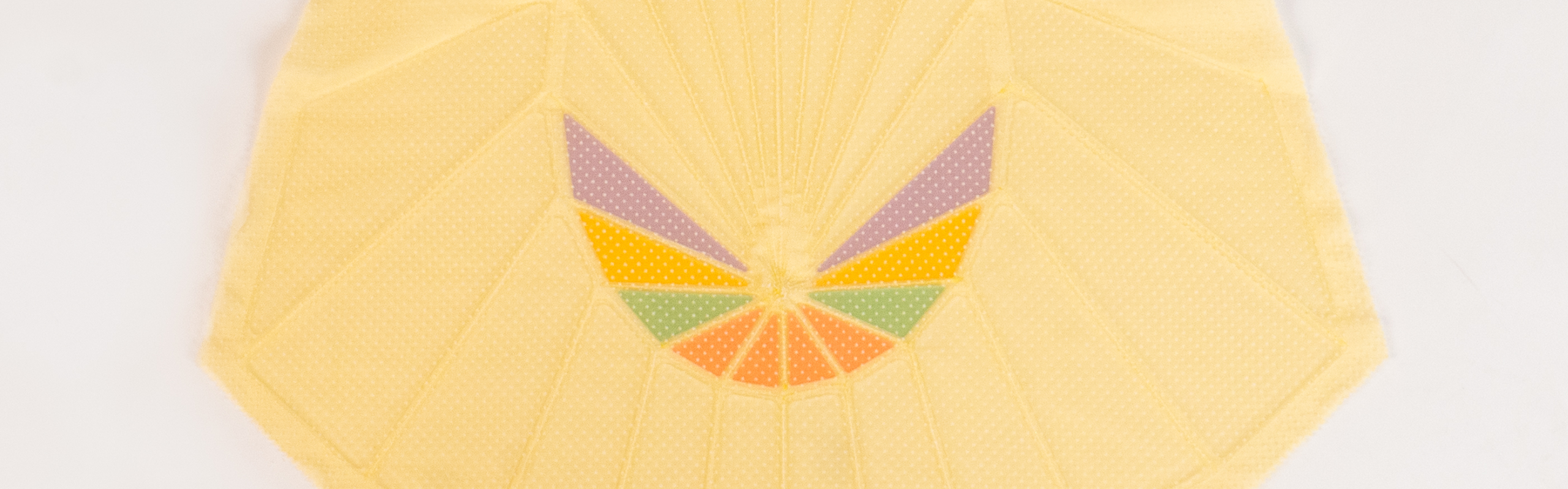
Flat-to-shape objects fabricated with a CNC sewing machine
Reimagining a machine traditionally used to make soft quilts to create functional, structural objects.
Abstract
Flat-to-shape, deployable objects allow for quick and easy need-based activation along with compact storage. We explore a novel method for fabricating functional objects using a large computer-controlled sewing machine traditionally used for quilting (11 ft / 3.4m wide), a process that is both rapid and scalable beyond the machine’s sewable area. We sandwich rigid form-defining materials such as plywood, or acrylic, between layers of fabric. The sewing process secures these layers together, creating soft hinges between the rigid inserts that allow the object to transition smoothly into its three-dimensional functional form with little post-processing.
Flat-to-shape, deployable objects allow for quick and easy need-based activation along with compact storage. We explore a novel method for fabricating functional objects using a large computer-controlled sewing machine traditionally used for quilting (11 ft / 3.4m wide), a process that is both rapid and scalable beyond the machine’s sewable area. We sandwich rigid form-defining materials such as plywood, or acrylic, between layers of fabric. The sewing process secures these layers together, creating soft hinges between the rigid inserts that allow the object to transition smoothly into its three-dimensional functional form with little post-processing.
I worked with Dr. Scott Hudson, Dr Lea Albaugh and Dr. Jim McCann.
Submitted to the ACM Conference on Human Factors in Computing Systems, CHI 2025.
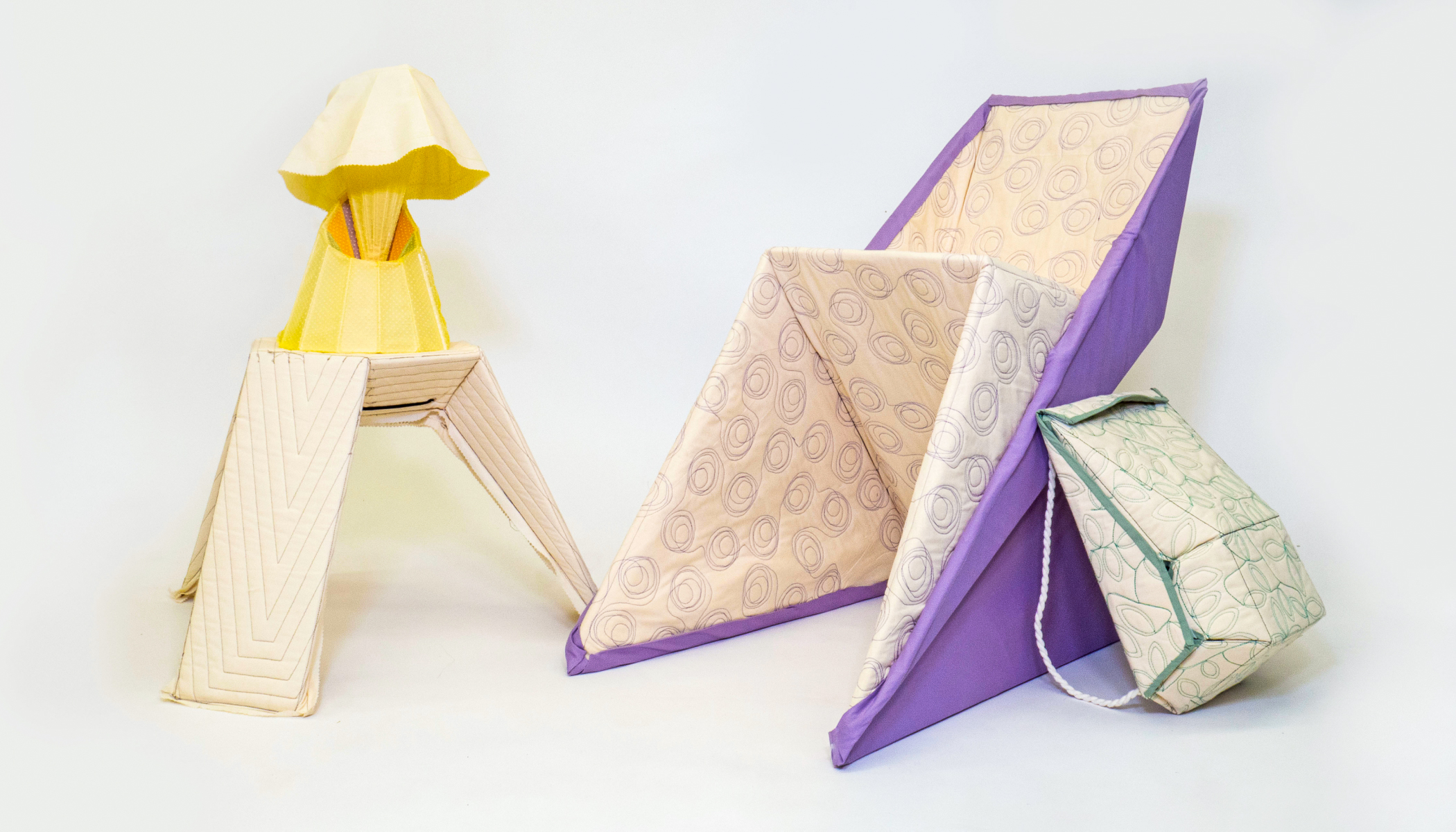



General method overview
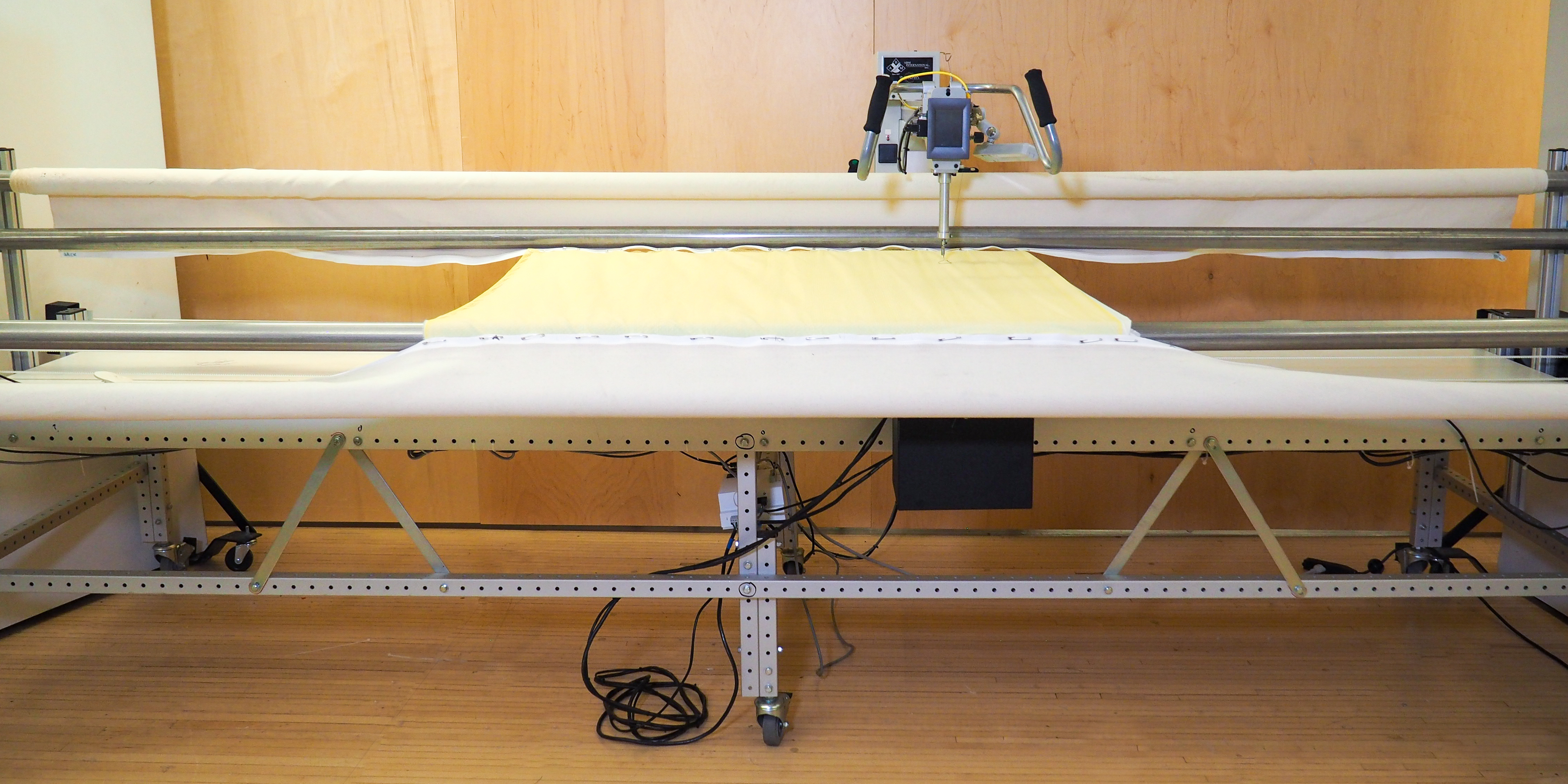
Modern computer-controlled sewing machines, which typically take the form of large-scale CNC quilting machines, offer precision, reliability, and scalability. However, their potential remains largely untapped beyond flat, fabric-based products like quilts. Our method utilizes the speed and scale of these machines to create high-quality, functional objects requiring minimal post-processing.
We specifically explore fabricating large-scale flat-to-shape deployable furniture and household objects. Such objects often can require intricate assembly processes, such as attaching metal hinges at each joint, or are limited by the size of the fabrication machine used, such as a 3D printer or laser cutter.
We specifically explore fabricating large-scale flat-to-shape deployable furniture and household objects. Such objects often can require intricate assembly processes, such as attaching metal hinges at each joint, or are limited by the size of the fabrication machine used, such as a 3D printer or laser cutter.
Our process utilizes the machine to sew pockets within layers of fabric into which rigid inserts are slid into. The pocket
is then closed off and the next one sewn, and this process repeated for the whole pattern.
This achieves a flexible fabric hinge between panels, enabling lightweight and easy transformation into three-dimensional shapes.
These rigid inserts can be customized—by adding LEDs, thicker materials for strength, or omitting them entirely for a more natural drape.
We also explore mechanisms like cords, magnets, and hook-and-loop fasteners to aid in transitioning and securing forms. The use of textiles in this process aligns with the context and functional needs of household items and adds a tactile and visual softness that complements interior environments.
We also explore mechanisms like cords, magnets, and hook-and-loop fasteners to aid in transitioning and securing forms. The use of textiles in this process aligns with the context and functional needs of household items and adds a tactile and visual softness that complements interior environments.
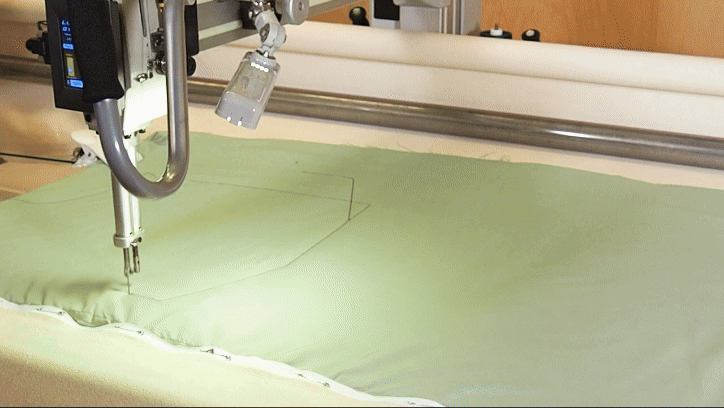
At production time, the fabric layers are held lightly tensioned between the front and back beams of the sewing machine, with the tension clips helping to stabilize them. We have the machine (under computer control) sew paths that partially enclose panel areas, pause the sewing process to insert the corresponding panel[s], and resume sewing to complete the enclosure[s]. These steps are repeated until all panels are enclosed!
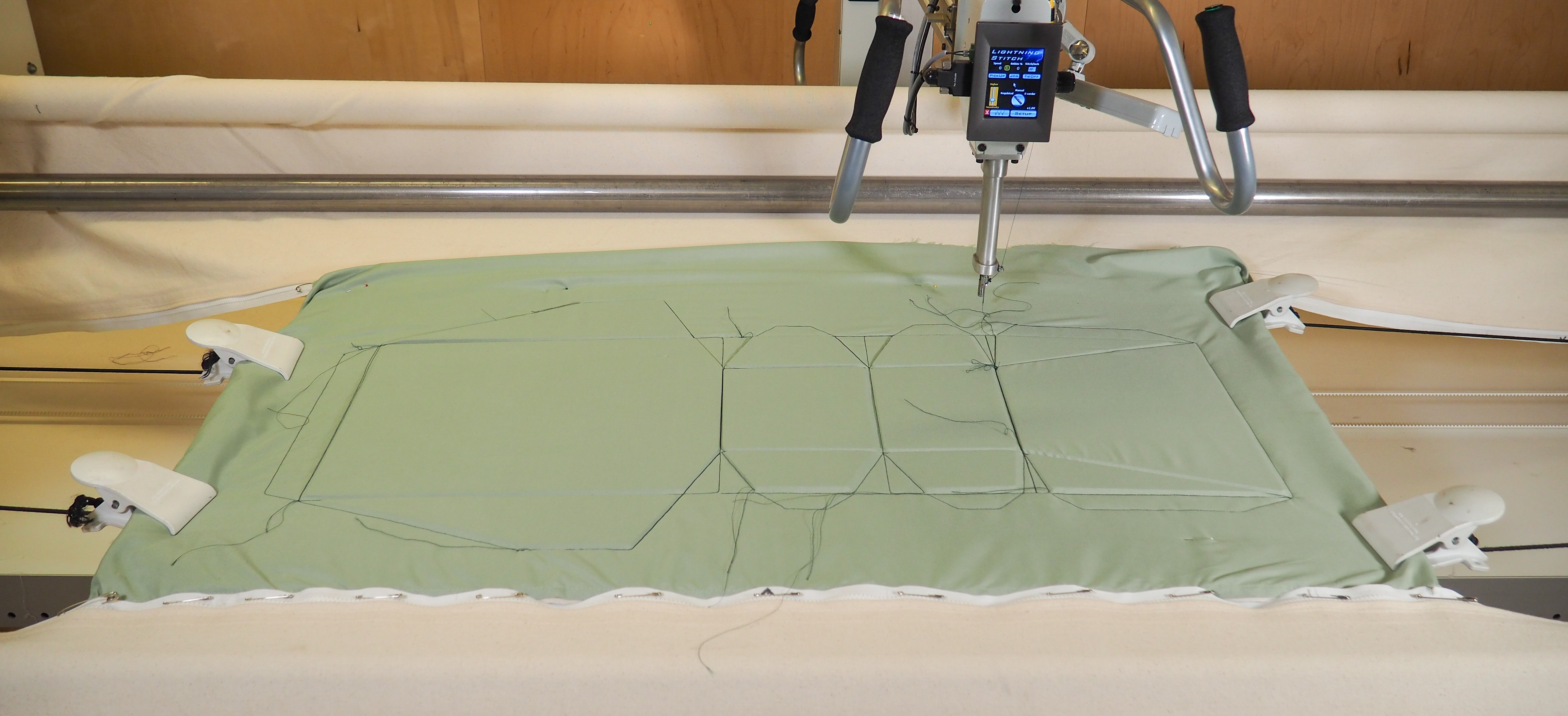
Backpack
The tendon cord system transforms the bag from flat to 3D and doubles as the straps. The cords lace through gusset panels between the main facets, pulling them flush and aligning the angled edges.
The main panels include 3/16" plywood inserts, while gusset panels remain flexible with hook-and-loop patches for selective attachment and locking.

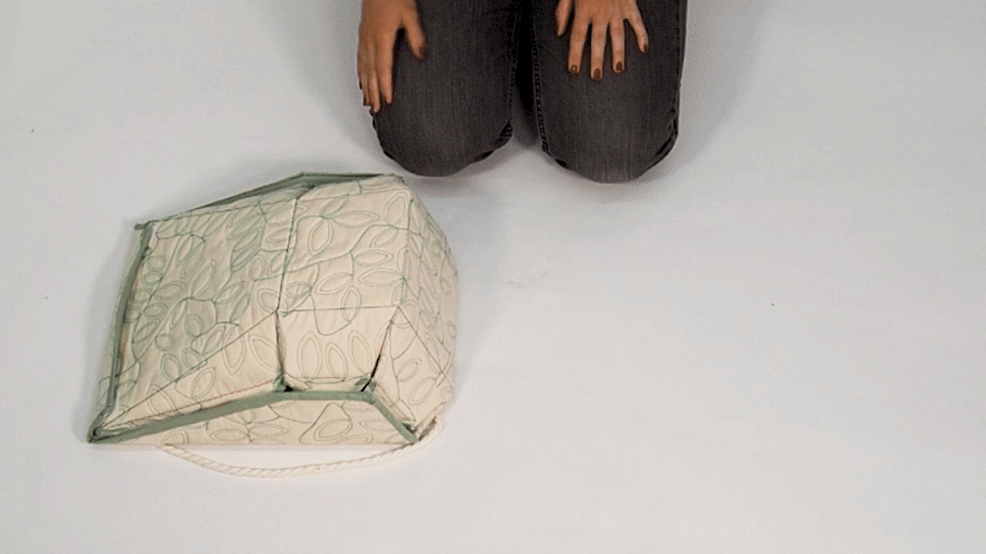
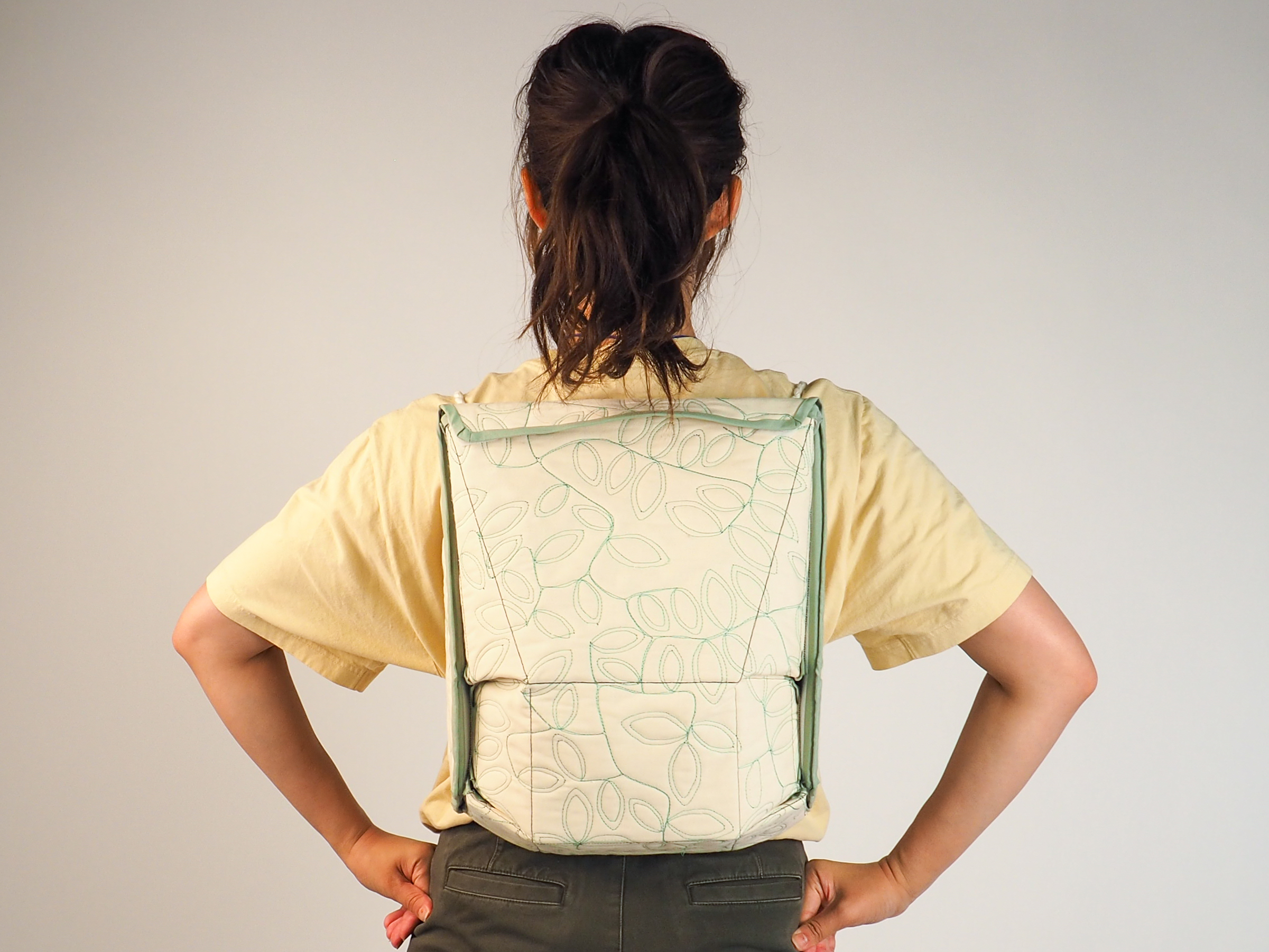

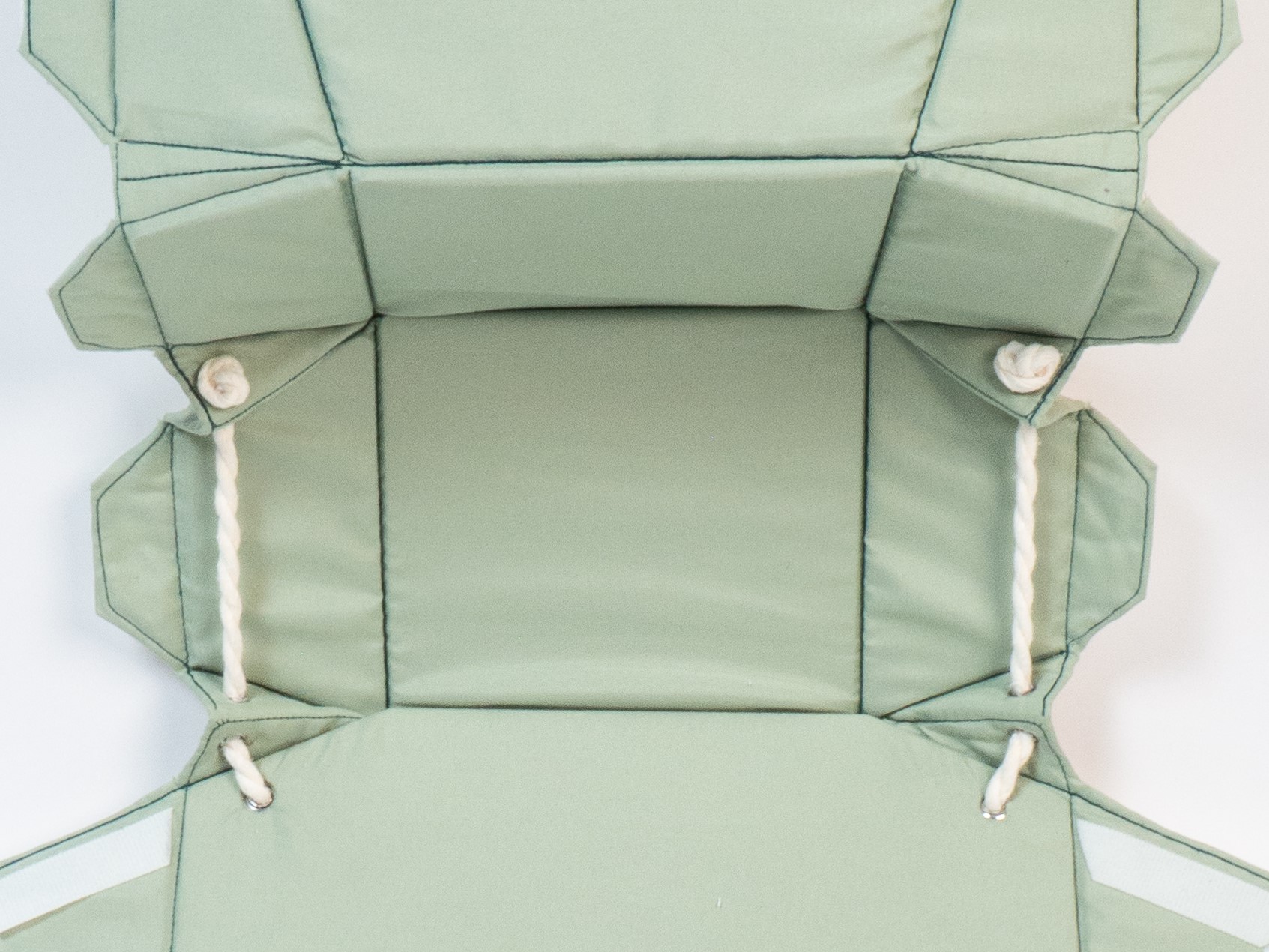
Lamp
The lamp is a modified 3D-printable pattern from BYU's Compliant Mechanisms Research Group, based on Robert Lang's Elliptic Infinity lamp.

We introduced four panel types for localized functions: lightweight plain acrylic panels at the base to highlight the fabric, cardstock-laminated panels in the inner ring for contrast, LED-integrated "active" panels in the upright section, and open spaces at the top for a graceful fabric drape as the lampshade.

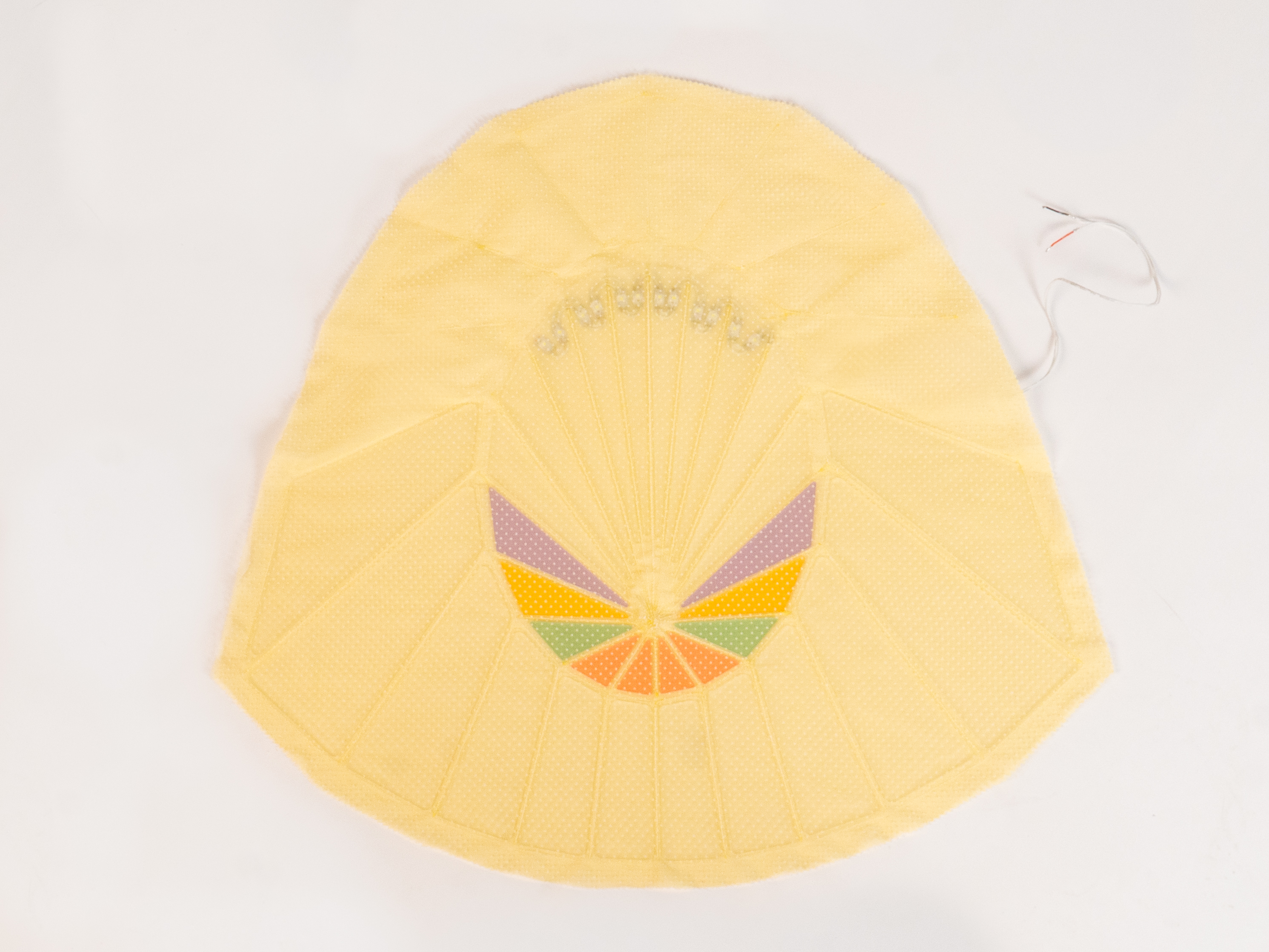
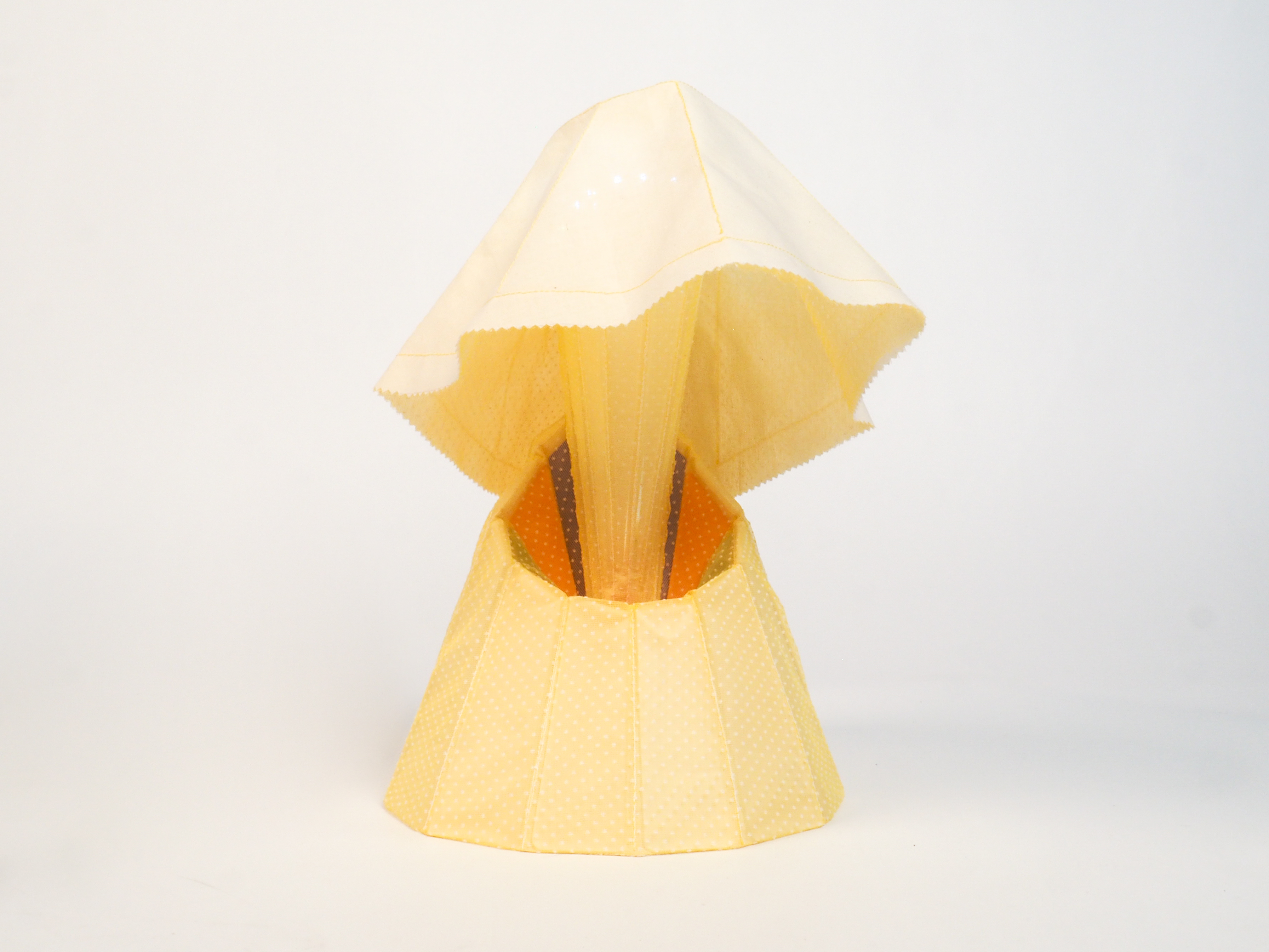
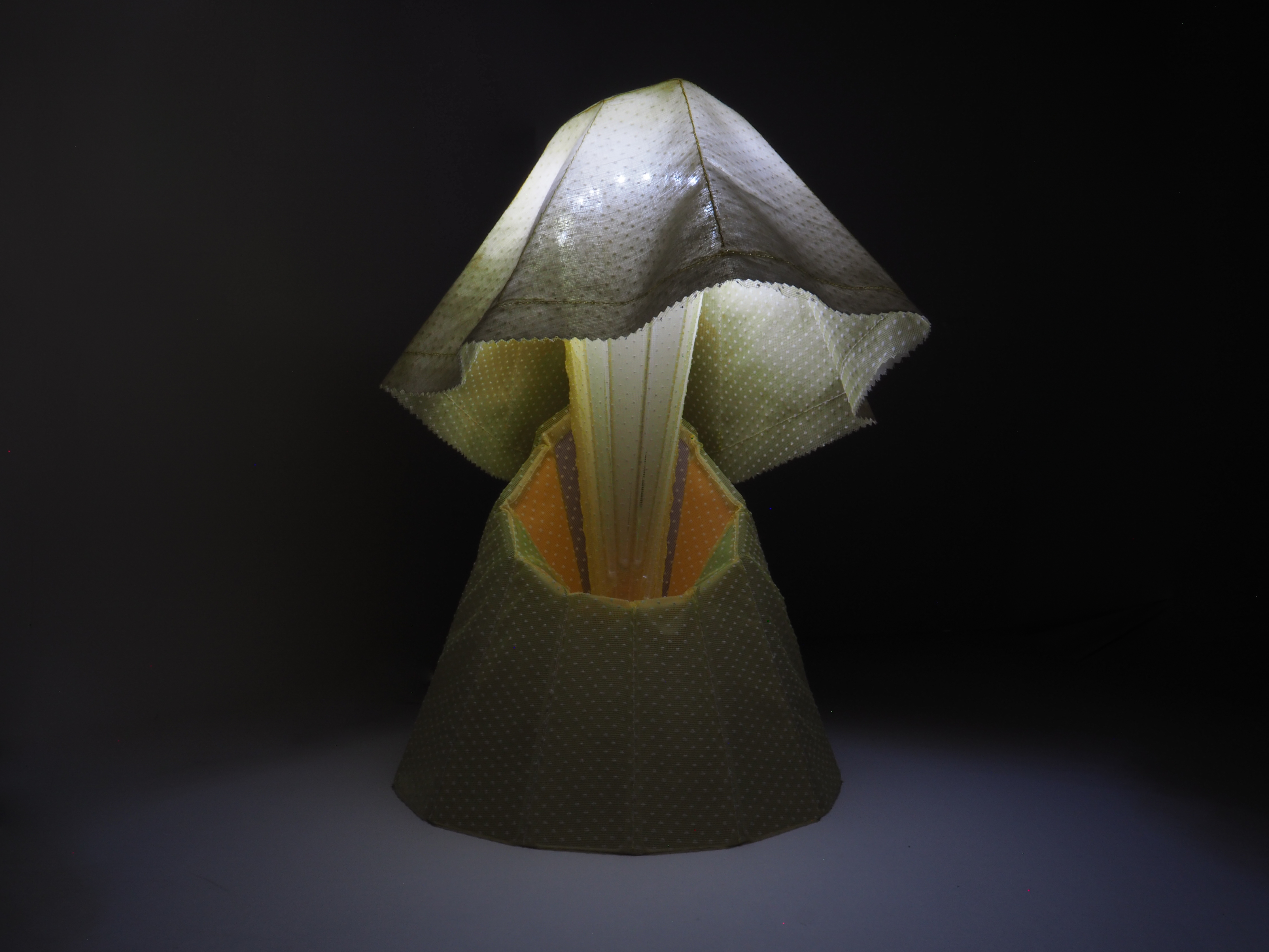
Lounge Chair
The lounge chair, measuring 60" by 56" when flat, is the largest object we fabricated with this method, designed to support an adult’s weight.
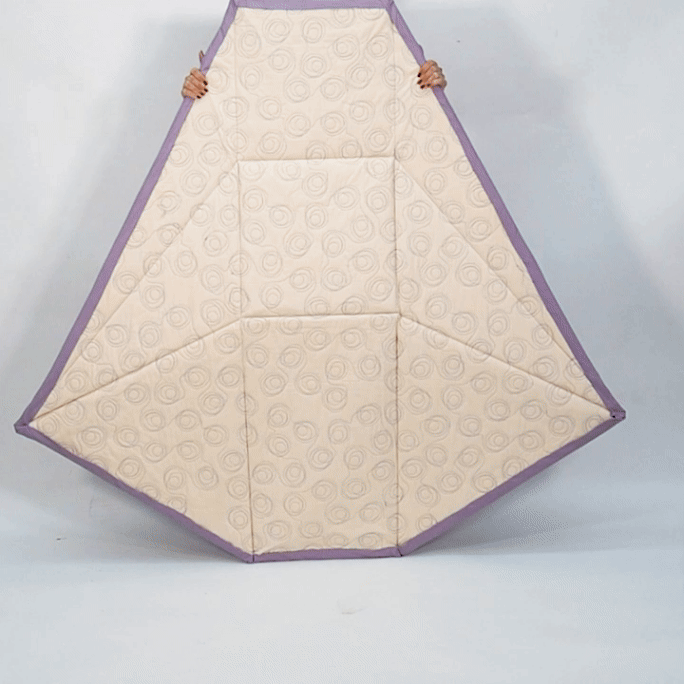

The insert panels, made from 1/2" plywood cut on a CNC router, are designed to meet face-to-face when deployed. Neodymium magnets, glued into milled pockets, allow the chair to "snap" into place, aligning the panels, while the fabric and panels carry the primary loads.

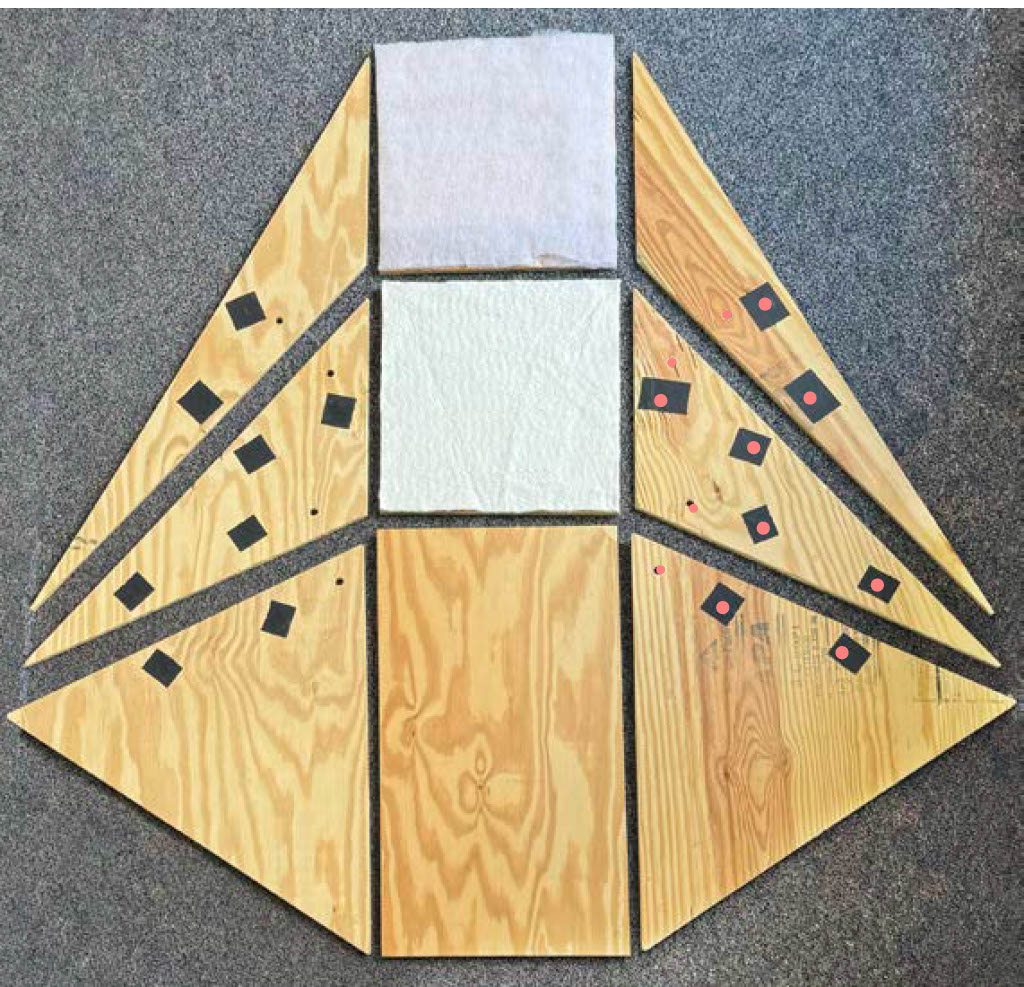
Side Table
The three-legged side table transforms from a flat 42" by 37" shape into a 17" tall table by pulling a tendon cord.
The cord acts on short rectangular struts, which meet in the center under the tabletop when fully deployed, stopping further movement. A spring cord lock secures the cord while the table is in use.
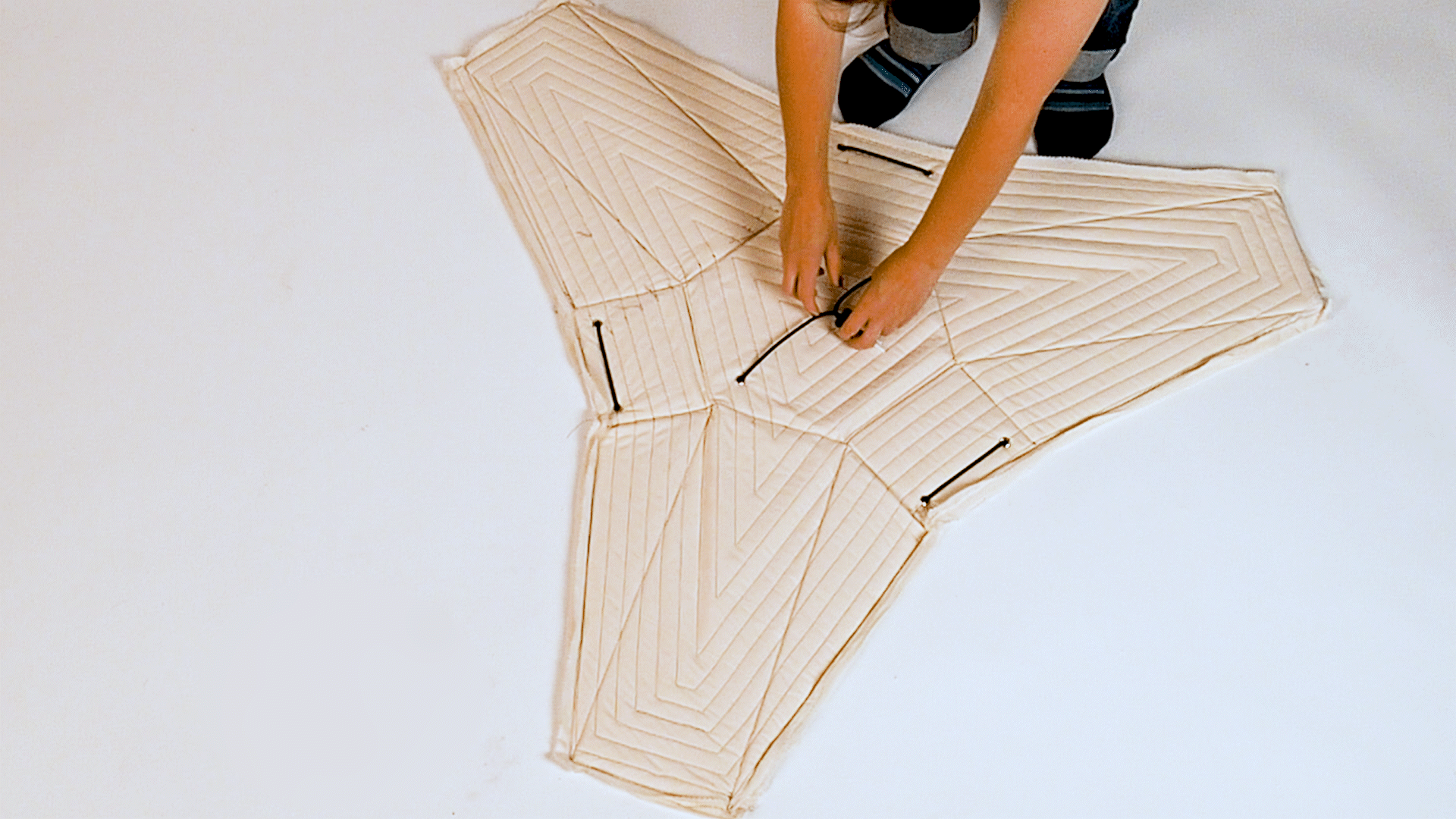
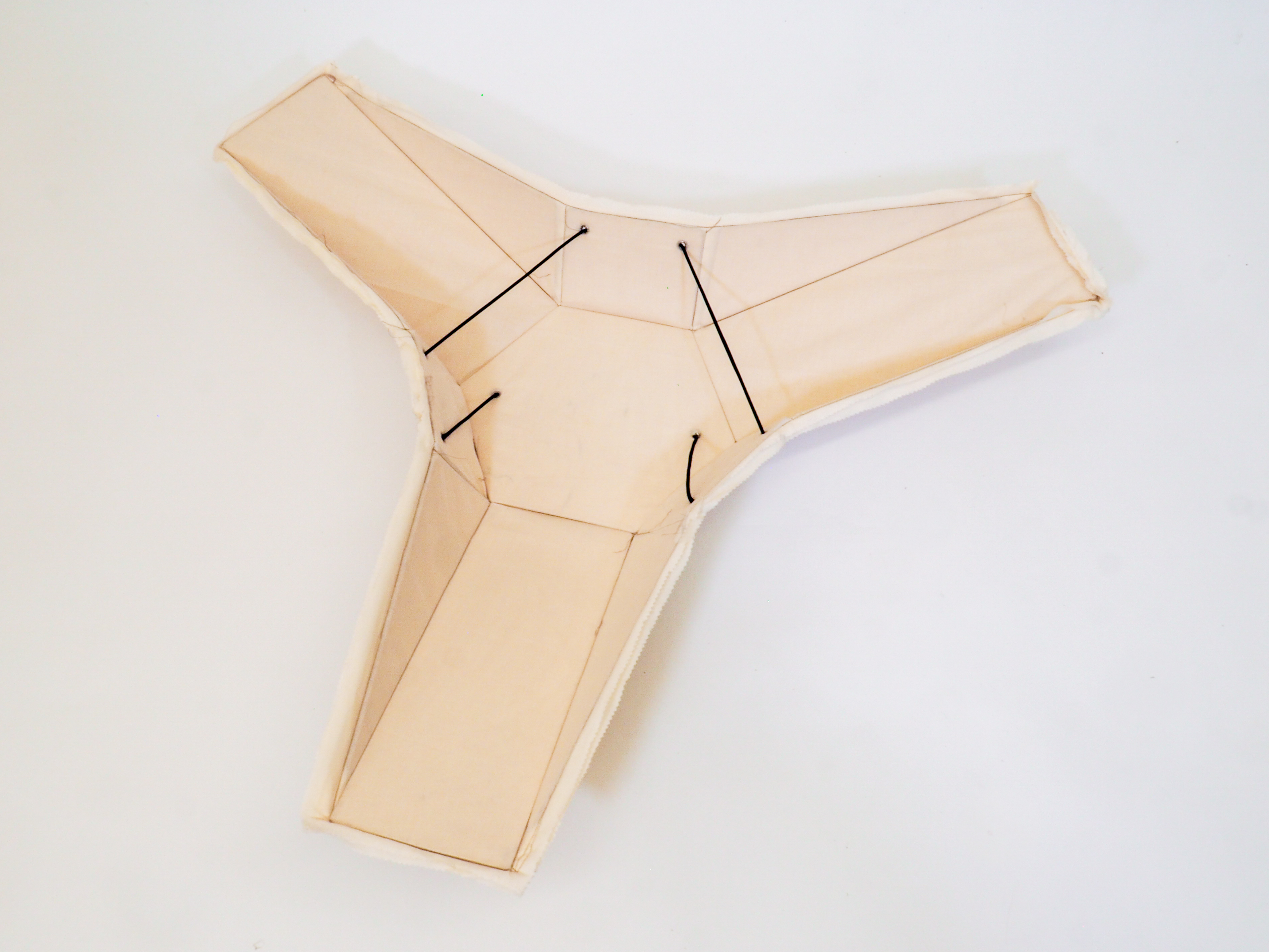
Technical process details
The exciting stuff! Figuring out how we can utilize this machine to make functional objects.
Human-machine collaboration: path & panel sequence
Instead of inserting all components before sewing, which can lead to distortion and misalignment, we used an incremental fabrication process that alternated between sewing pockets and placing inserts. This method ensured snug placement with narrower margins, guided by the pattern.
To streamline our workflow, we implemented two strategies. First, we designated “last edges” for pockets to ensure proper positioning of each insert; simple shapes like rectangles allowed for any edge to be a last edge, while complex shapes required careful selection. Second, we worked through the pattern directionally, either outward from a point or from one side to the other, to maintain logical sequencing and optimize sewing area use.
Lastly, we Eulerized the sewing paths by doubling the edges, enabling the machine to backtrack and sew each path twice, which created a continuous and uninterrupted process.
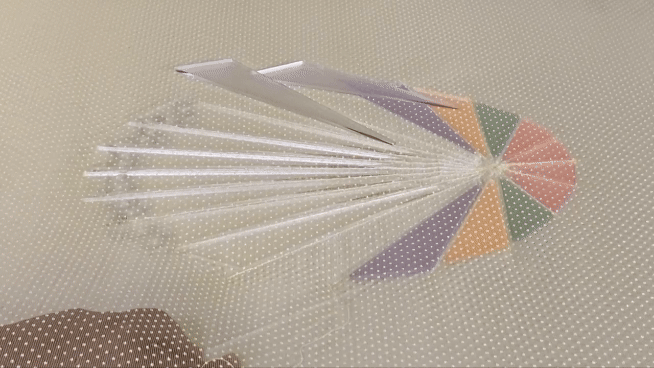
Panel Sizing
The inserts in our designs are inset from the edges of their sewing path. This is both essential for fabrication and allows for additional flex in the system. Because our fabrics are not stretchy, an offset of half the thickness of the insert material is the minimum necessity to allow the insert to fit in the fabric pocket.
Any additional margin will allow a greater range of motion to the fabric hinge. However, the
inherent slight stretchiness of fabric (and the mechanical advantage afforded by the panels) makes using this effect to precisely control folding angle impractical in our tests.
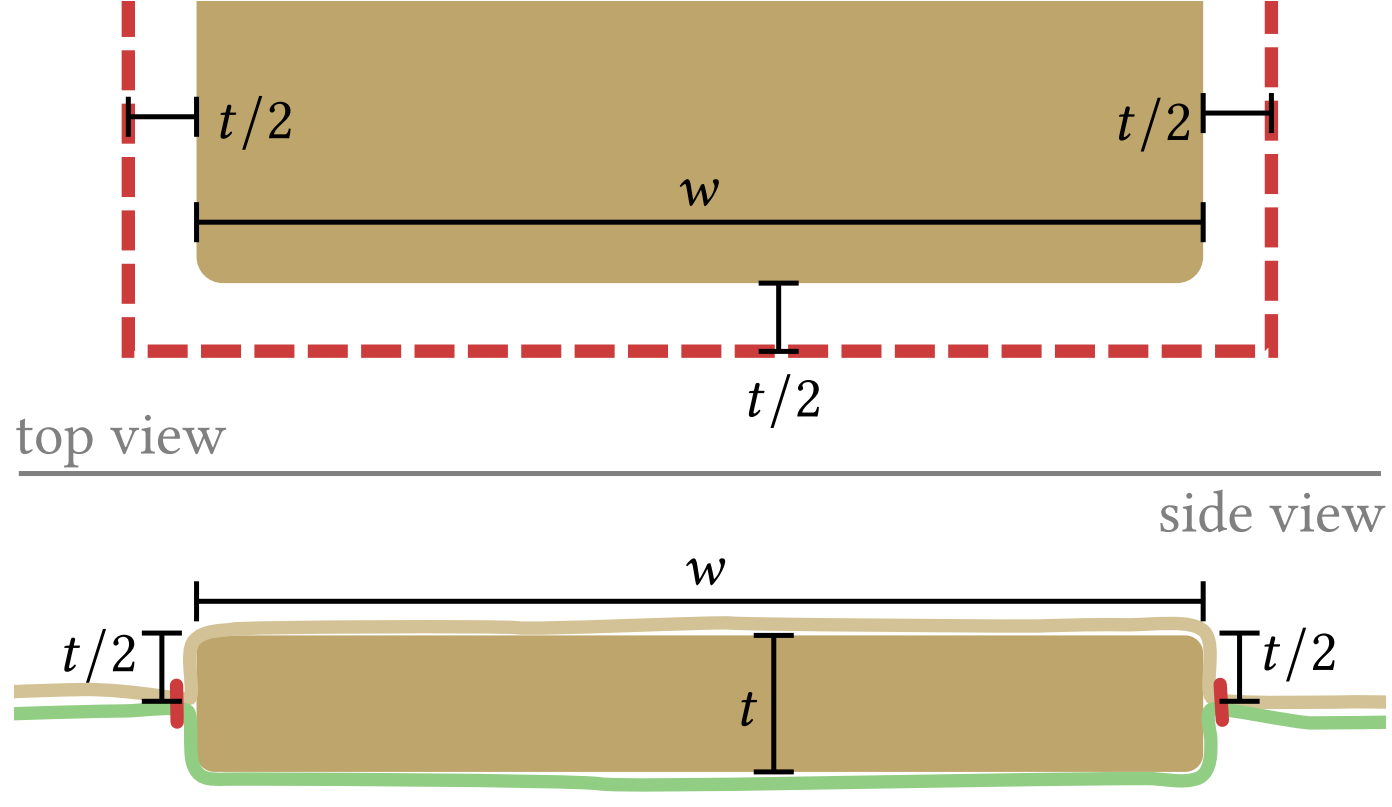
Scaling up
The long-arm quilting machine used in this project has a reliable sewing area of 11 feet by 25 inches. Under the typical
use of the machine to make soft quilts, the fabric runs over the front beam and is rolled up underneath.
This approach is unsuitable for our process, as completed areas include rigid panels that can't be rolled up. Instead, we use a height-adjustable table, matching the machine's front beam height. Sewn material is draped over the table, and a weighted rod threaded through the fabric edge creates tension, maintaining alignment during stitching.
This approach is unsuitable for our process, as completed areas include rigid panels that can't be rolled up. Instead, we use a height-adjustable table, matching the machine's front beam height. Sewn material is draped over the table, and a weighted rod threaded through the fabric edge creates tension, maintaining alignment during stitching.


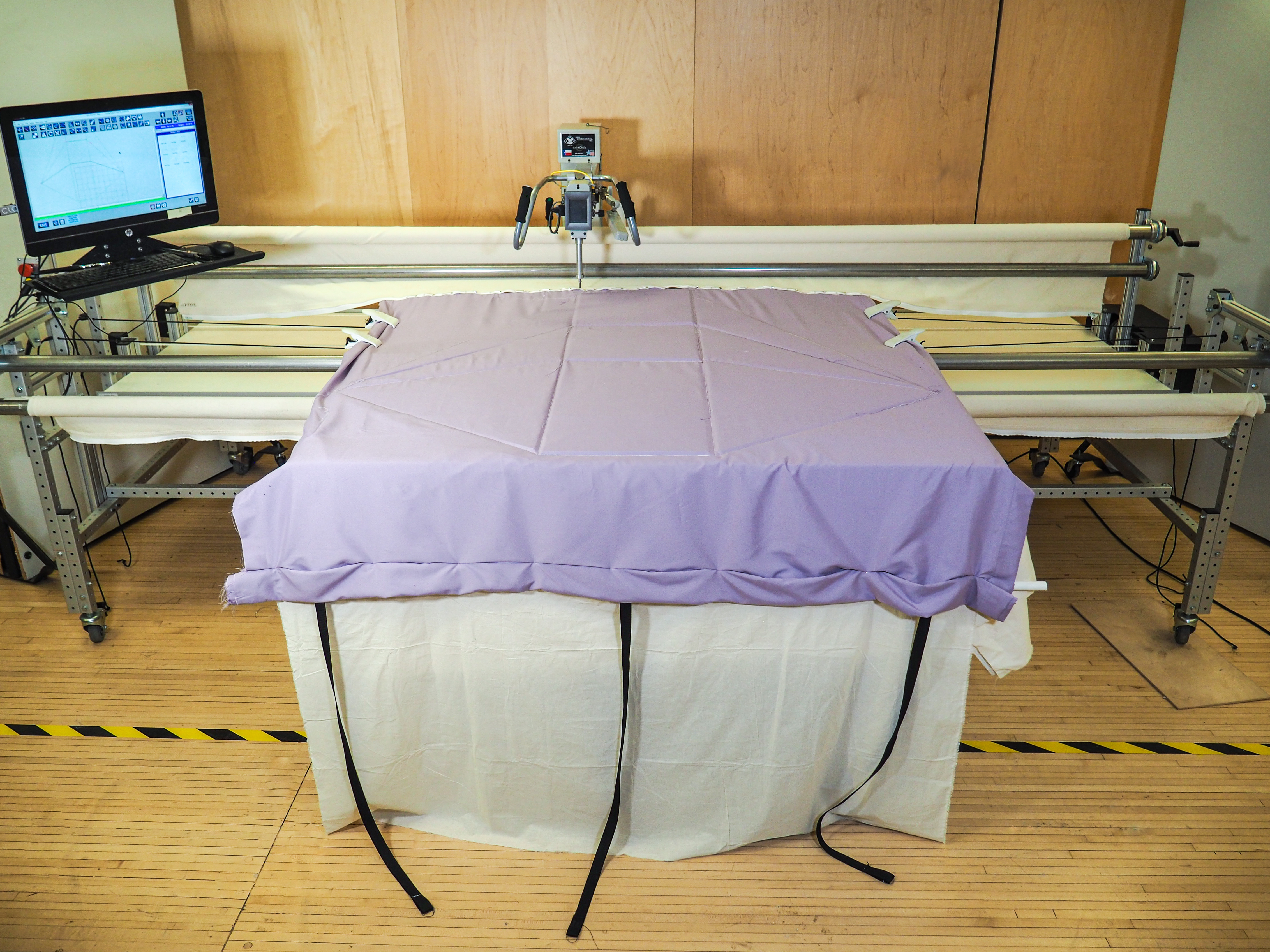
Initial discovery process
With the starting goal of the project being pushing the boundaries of what a Longarm Quilting machine can fabricate, I undertook a tiral and error, research-through-design, process of playing with different sewing and gathering methods and studying their effects.

Iterating on geometry and fabrication methods
Here are some of my experiments figuring out successful processes and forms!
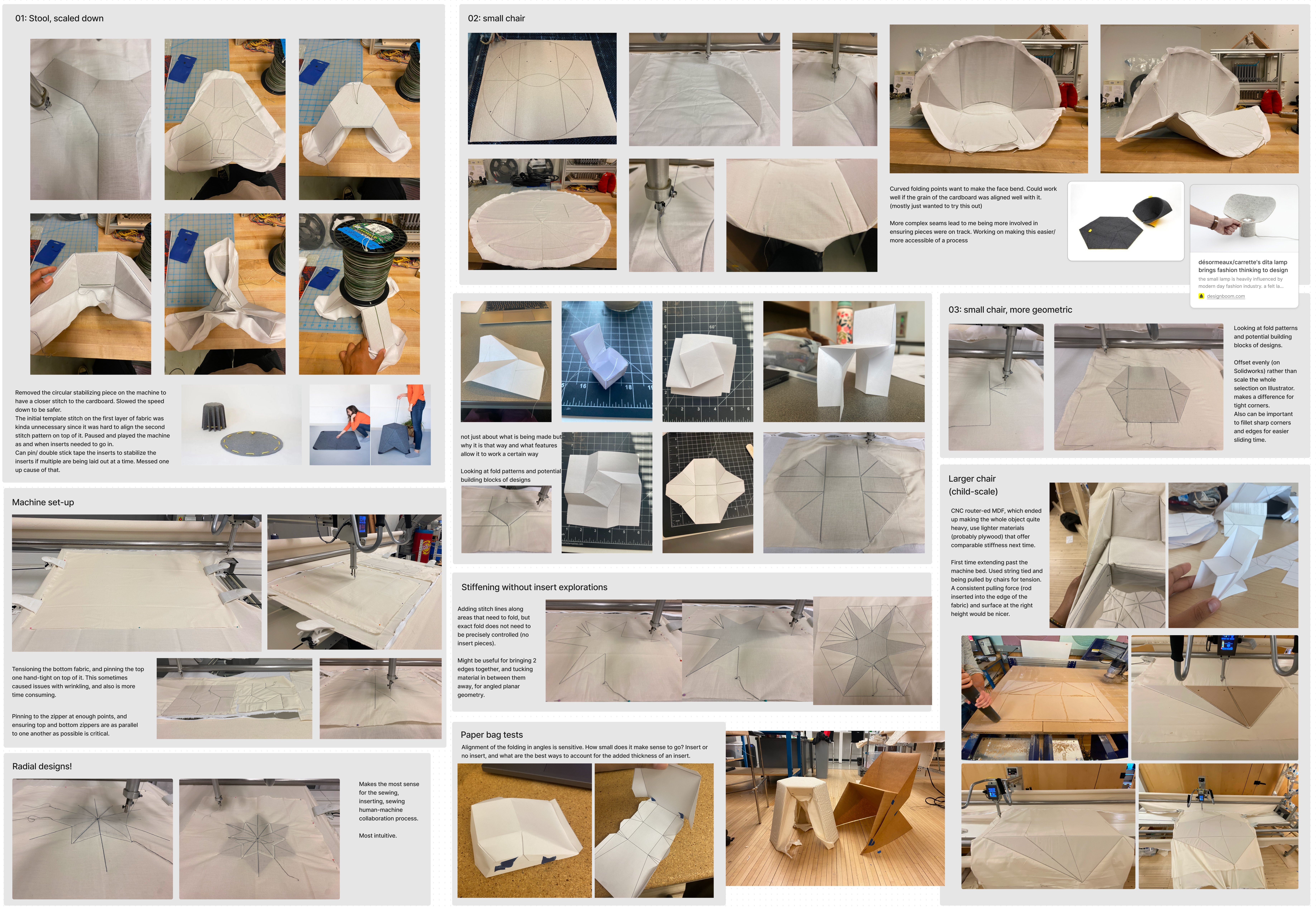
10. ~Machine Maintenance ~
Mid-project we ended up needing to move the machine (~13’ by 5’) from it’s original home to the HCI lab across campus. Dismantling and reassembling it was a valuable learning experience, revealing design details and tweaks to improve its performance for my project. Here is some documentation of the move :D

01. Taking the sew head off
(it’s really heavy and took 5 people!)
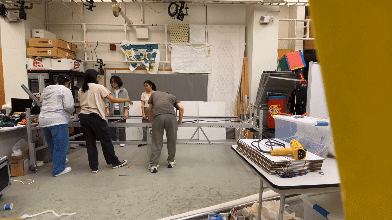
02. Taking apart the structure
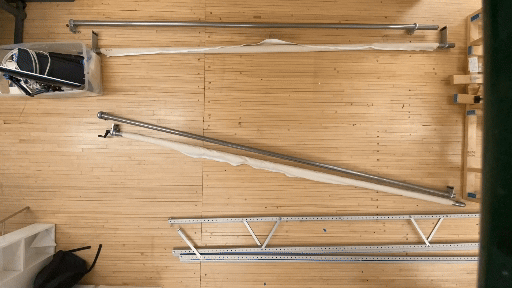
03. Putting it all back together in the new lab
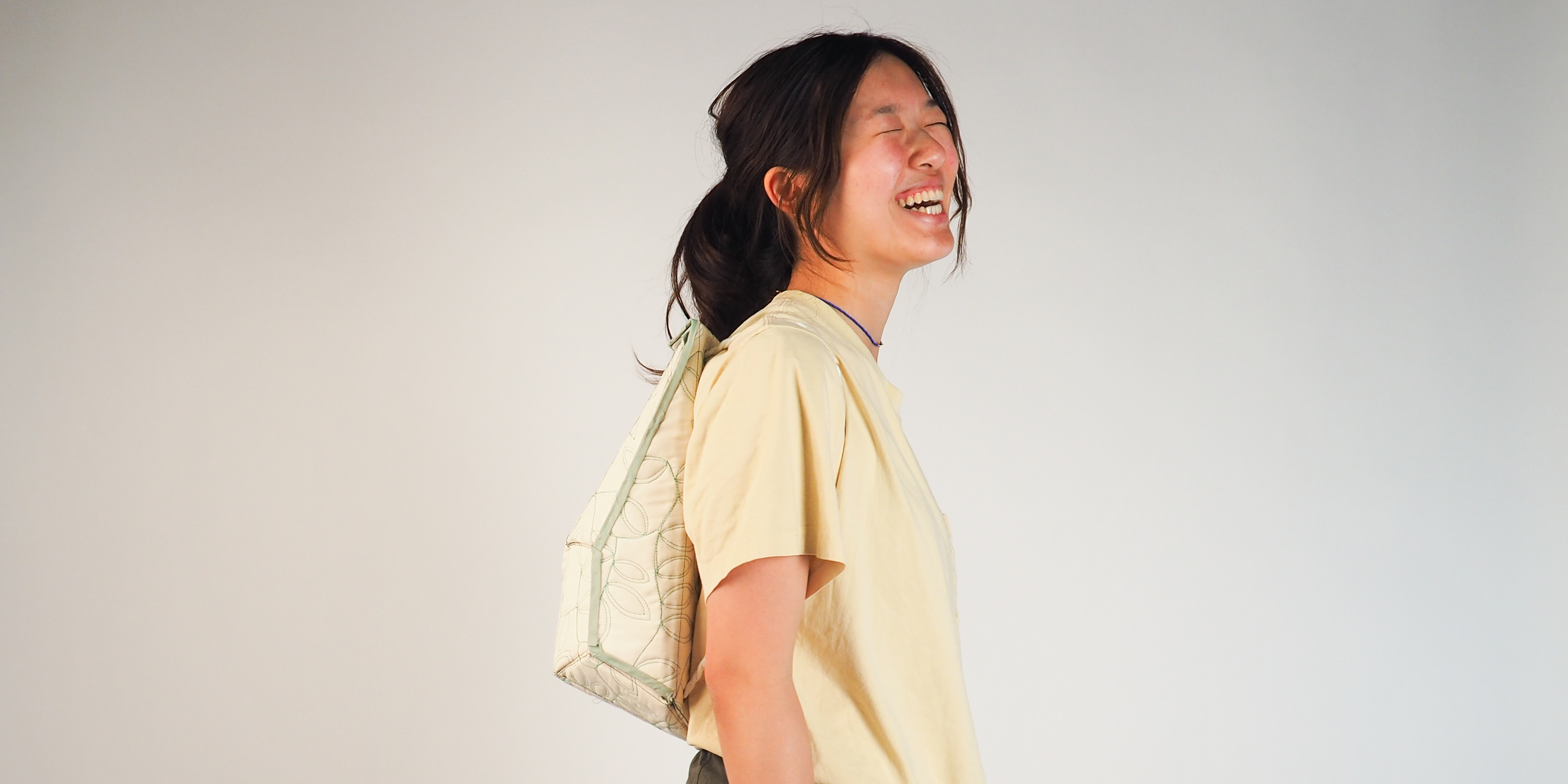
Thanks for visiting <3