Carnegie Mellon Racing, Driver Systems
We are a team of ~80 students who design, test, and build an electric race car from the ground up every year to compete in the Formula SAE competition.
Last year I led the driver-systems subteam of ~10 students working on the pedals, steering wheel, dashboard, seat, headrest, impact attenuator and firewall. I worked on adjustability and accessibility of driver contact points, mechanical optimizations, and exploring new manufacturing methods while balancing integration, timeline and budget constraints. I’ve also worked on R&D experiments that validated the team’s transition from a steel tube chassis to a carbon fiber monocoque.
I love being hands-on, collaborative, and working accross the full start to finish process of making things on the team.
Last year I led the driver-systems subteam of ~10 students working on the pedals, steering wheel, dashboard, seat, headrest, impact attenuator and firewall. I worked on adjustability and accessibility of driver contact points, mechanical optimizations, and exploring new manufacturing methods while balancing integration, timeline and budget constraints. I’ve also worked on R&D experiments that validated the team’s transition from a steel tube chassis to a carbon fiber monocoque.
I love being hands-on, collaborative, and working accross the full start to finish process of making things on the team.
Engineering design, rapid prototyping, ergonomics, DFM/DFA, component testing & validation, composite manufacturing, manual machining, CAD, leadership & teamwork
2022 - Present
2022 - Present

24e Steering Wheel !
As one of the primary contact points, the steering wheel was designed with a focus on ergonomic comfort, structural integrity, and efficient packaging. With the smallest PCB we've ever used, I carefully packaged components to optimize space while preserving both function and aesthetics. Throughout the process, I collaborated closely with drivers and electrical engineers to ensure the design met both user and technical requirements.

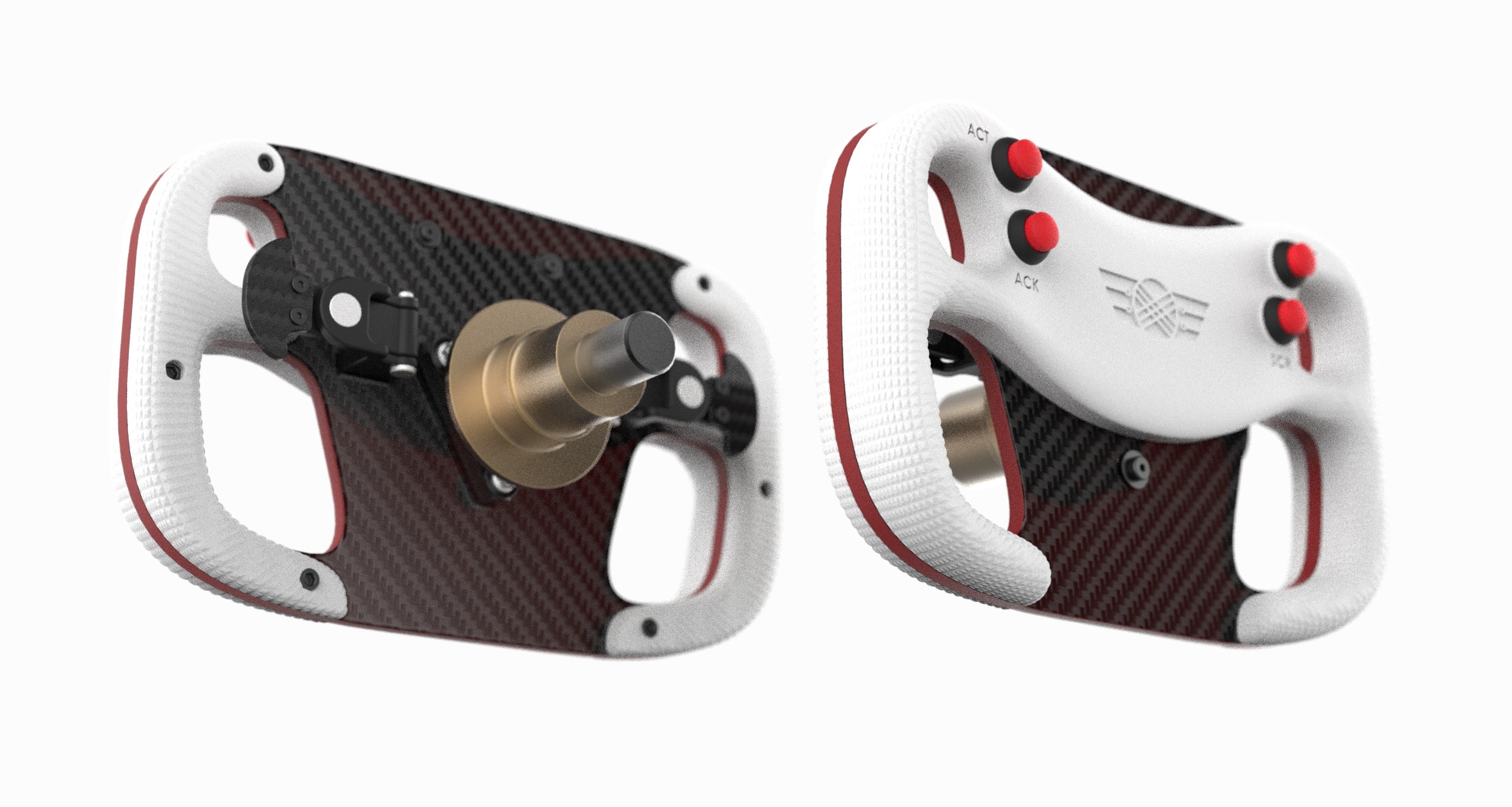
Design overview
The steering wheel's carbon-fiber main plate, with a Nomex core and solid carbon hardpoint, provides a structural base for mounting components that can withstand torque inputs. It connects via a 10-pin electronic quick-disconnect, with a 3D-printed enclosure for electronics and rear grips enhancing ergonomics.
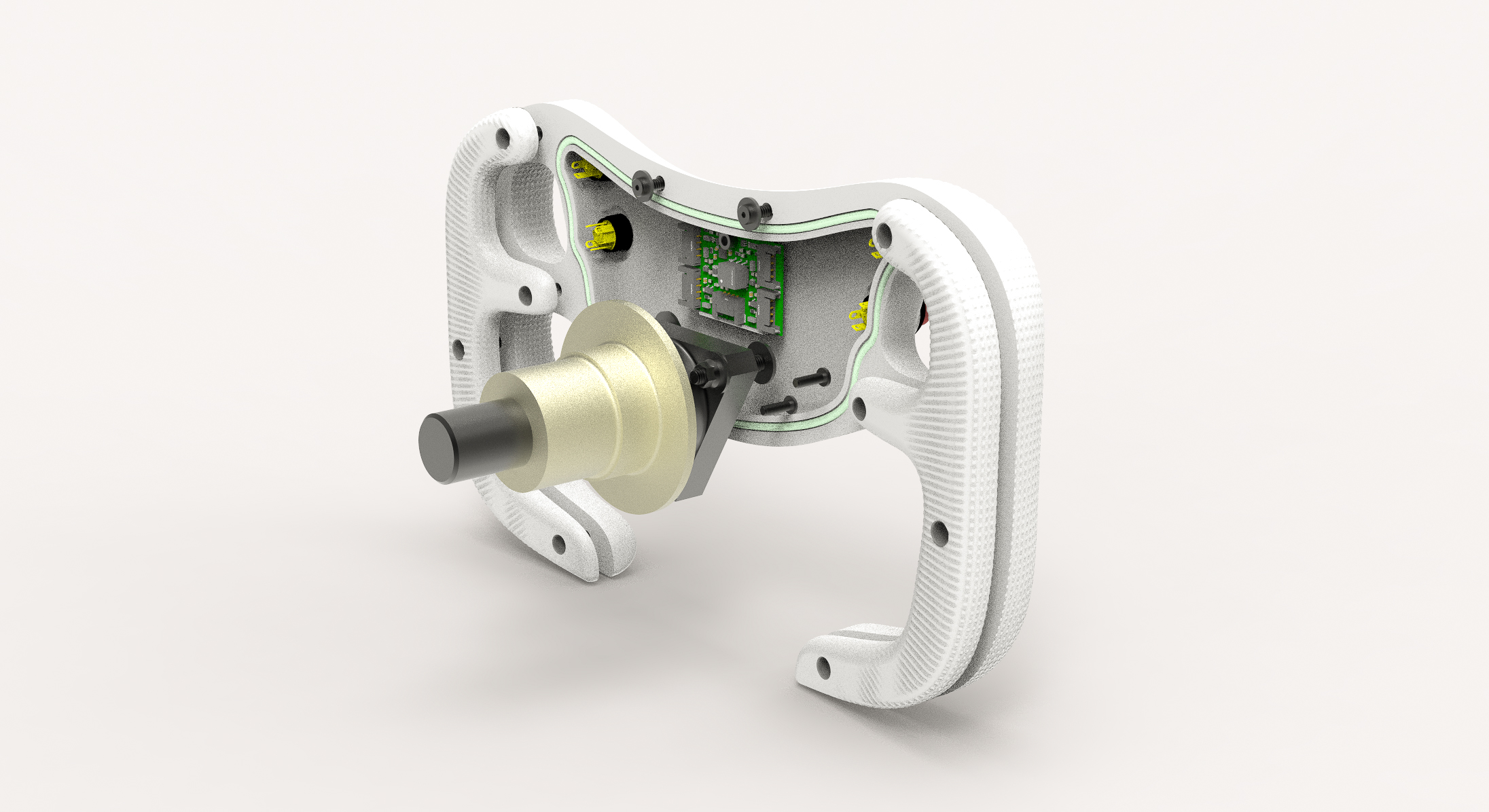
With a very size-efficient custom daughter board going into the wheel this year, I aimed to design the enclosure that
efficiently packaged electronics.
To ensure reliable waterproofing, I replaced gasket sheets with an o-ring for a more predictable solution.
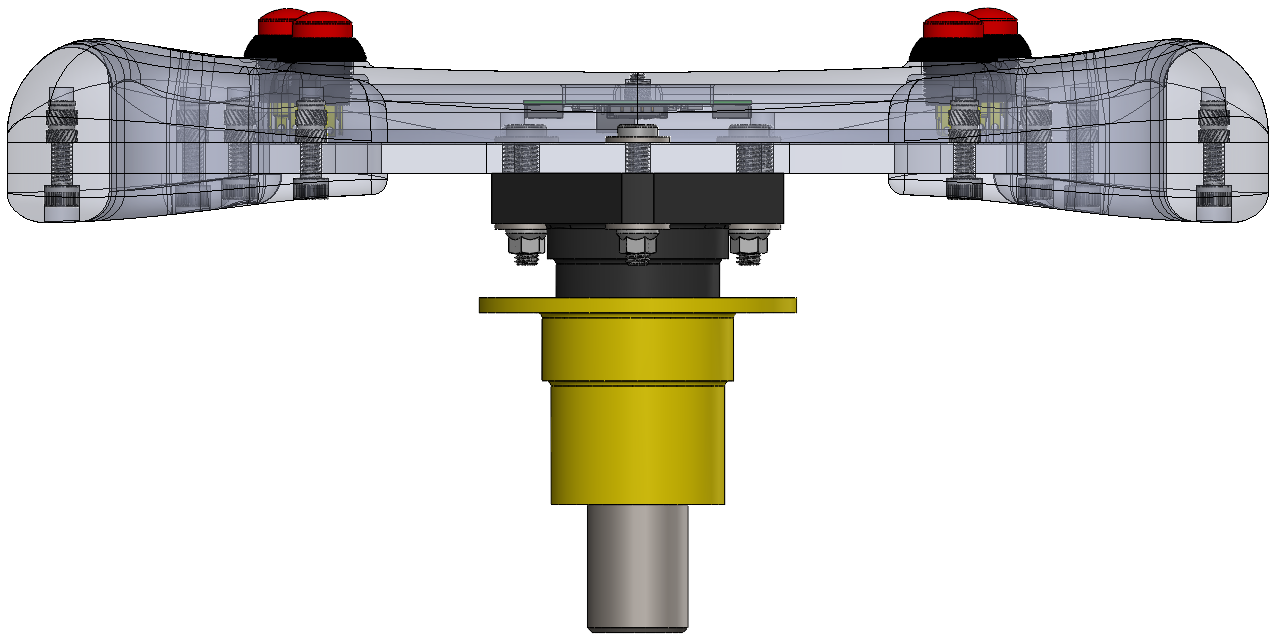
To create a rougher grip and avoid using tennis racket tape and sticker labels, I experimented with embedding texture and labels directly into the printed surface.
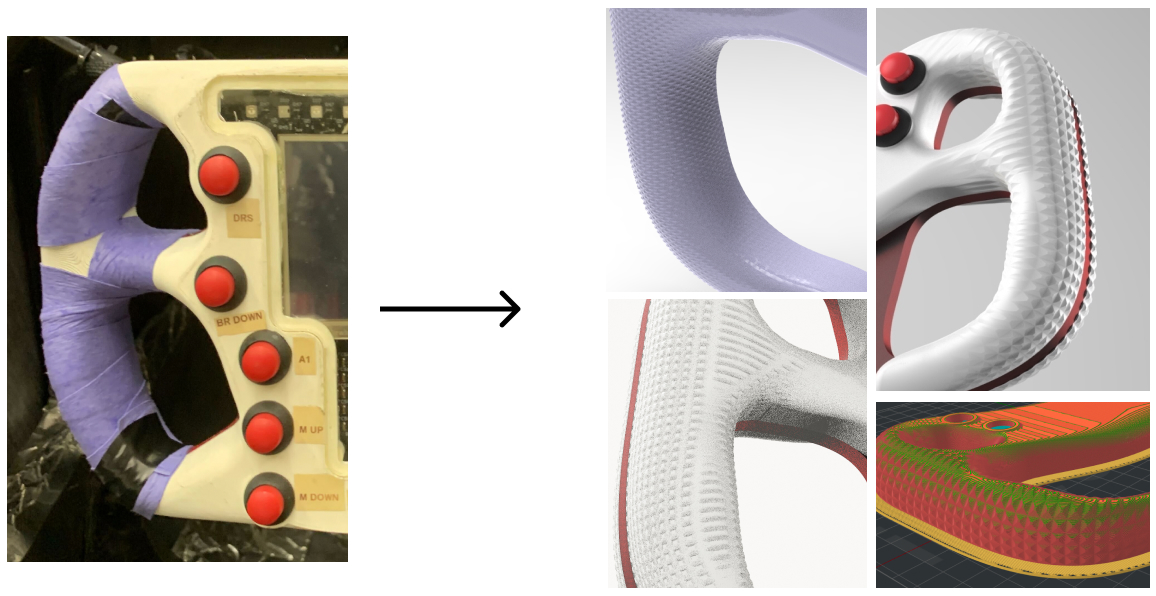
Some of my sketches during the ideation and design process.
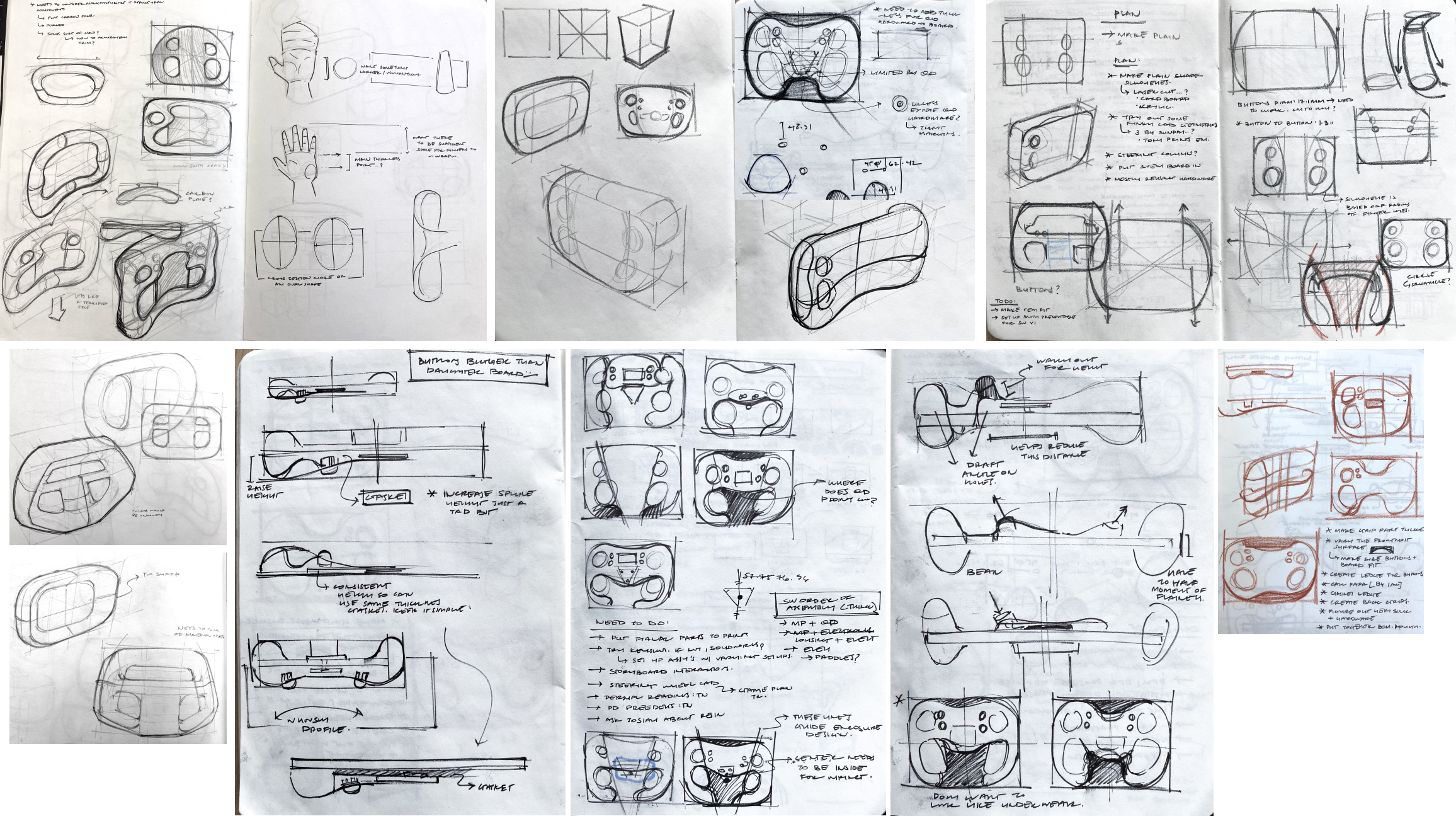
Constraints & validation
The steering wheel was designed in collaboration with other systems on the car. We conducted tests on previous cars and our ergonomics rig to establish how much the wheel could move relative to the driver, informing the geometry of the steering column, front roll hoop and dashboard, and other driver systems.
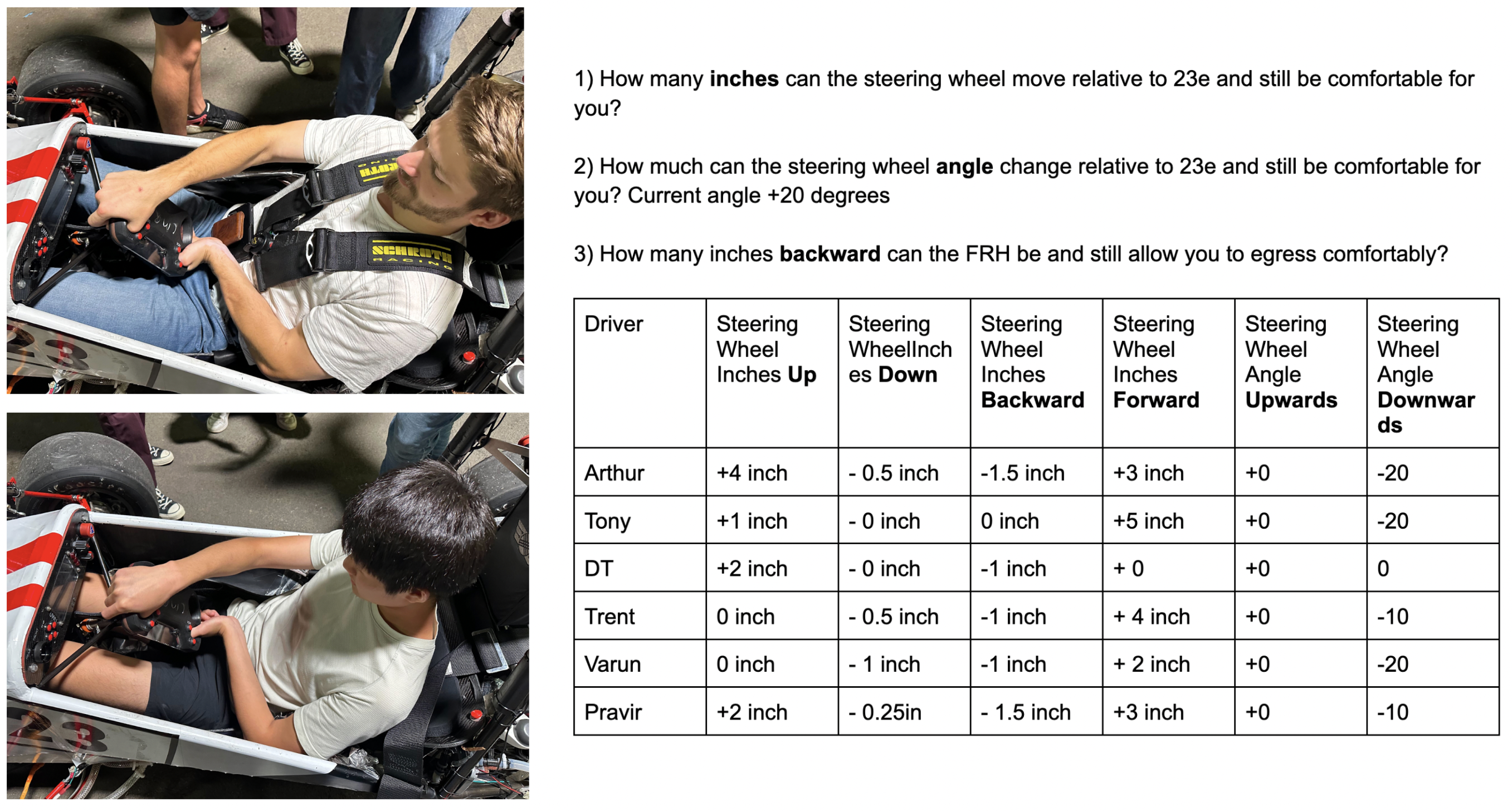
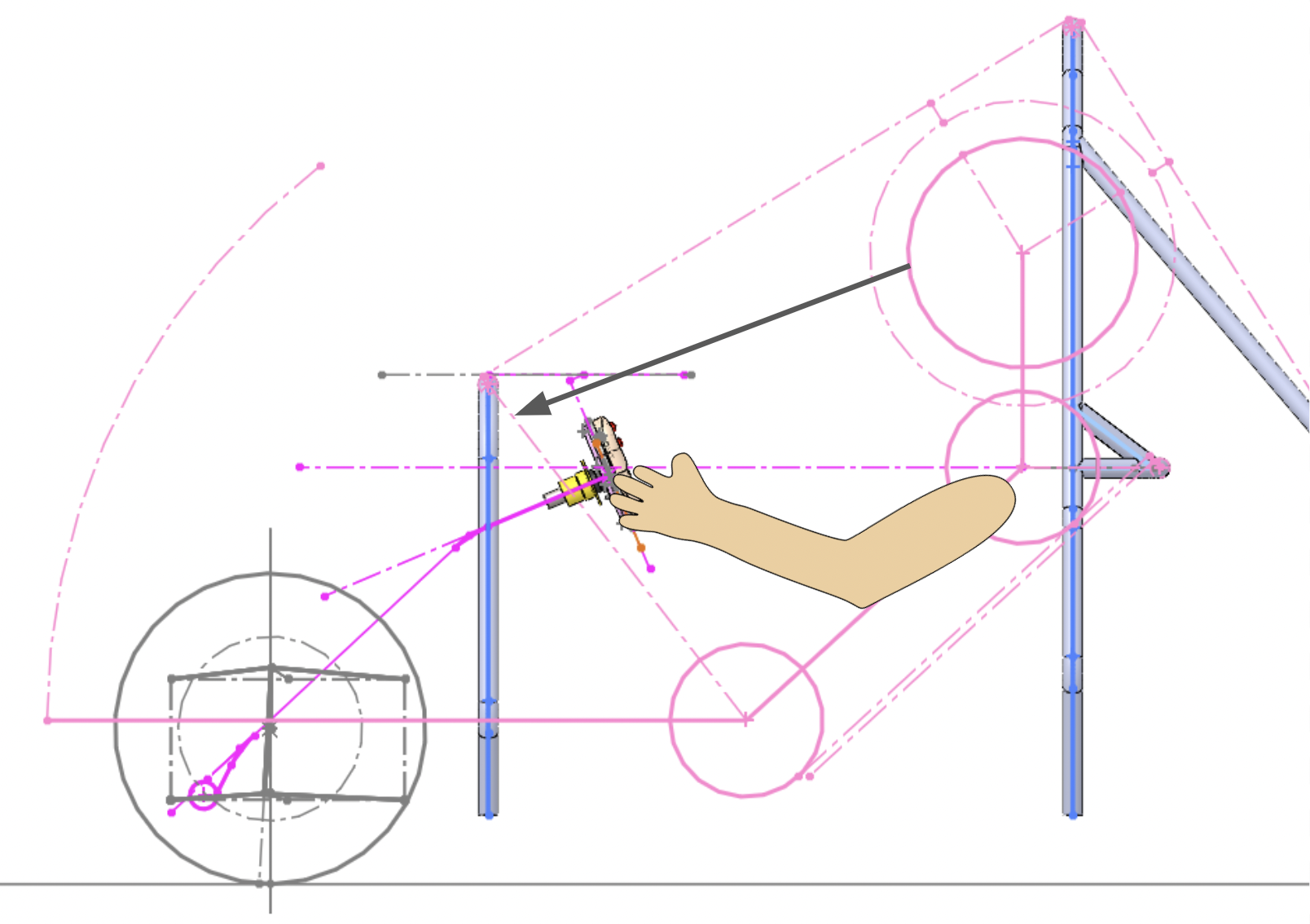
I worked with drivers and software engineers to ensure quick access to key controls on the steering wheel and dashboard for easy mode testing during track sessions.
The wheel houses essential buttons, including PTT for radio, ACK for message acknowledgment, SCR for dashboard screens, and an ACT button for functions like DRS positioning or launch control.

Crafted rough foam prototypes and iterated adjustments based on hand-feel, measurements, and feedback from previous steering wheels. This helped establish a set of informed baseline measurements before transitioning to CAD.
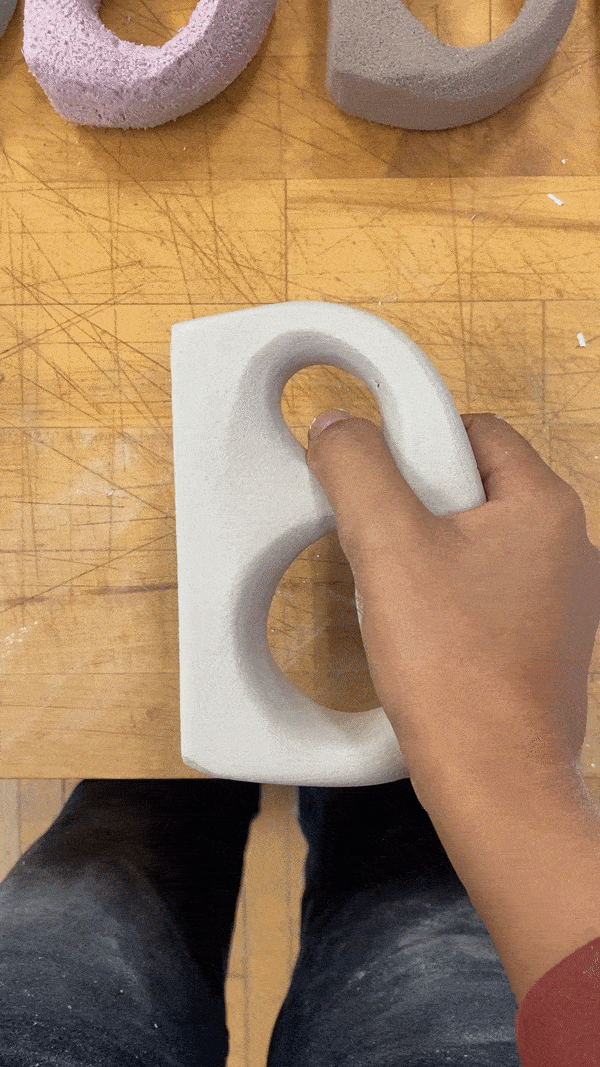
Throughout the design process, I 3D printed and laser cut models to gather driver feedback on comfort, button accessibility, and clearances.
These ergonomic studies included questions like, "What are pain points at a full turn?" and "How much more space would you like for your pinky finger?" This feedback helped refine the form to better suit driver preferences and bridge the gap between CAD models and real-world feel.
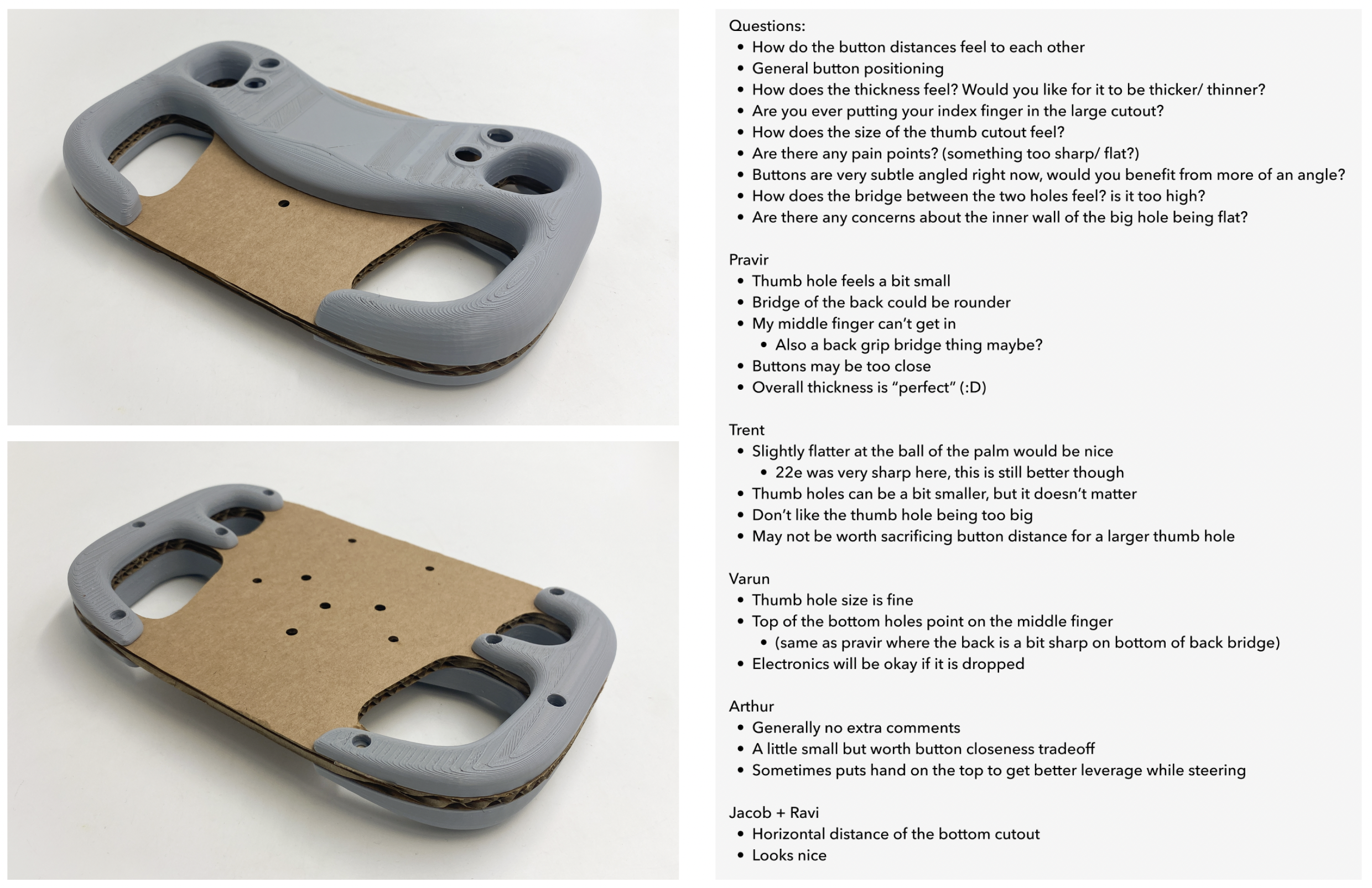
Manufacturing & assembly
The 3D printed enclosure and grips on a SLS printer with Nylon 12.
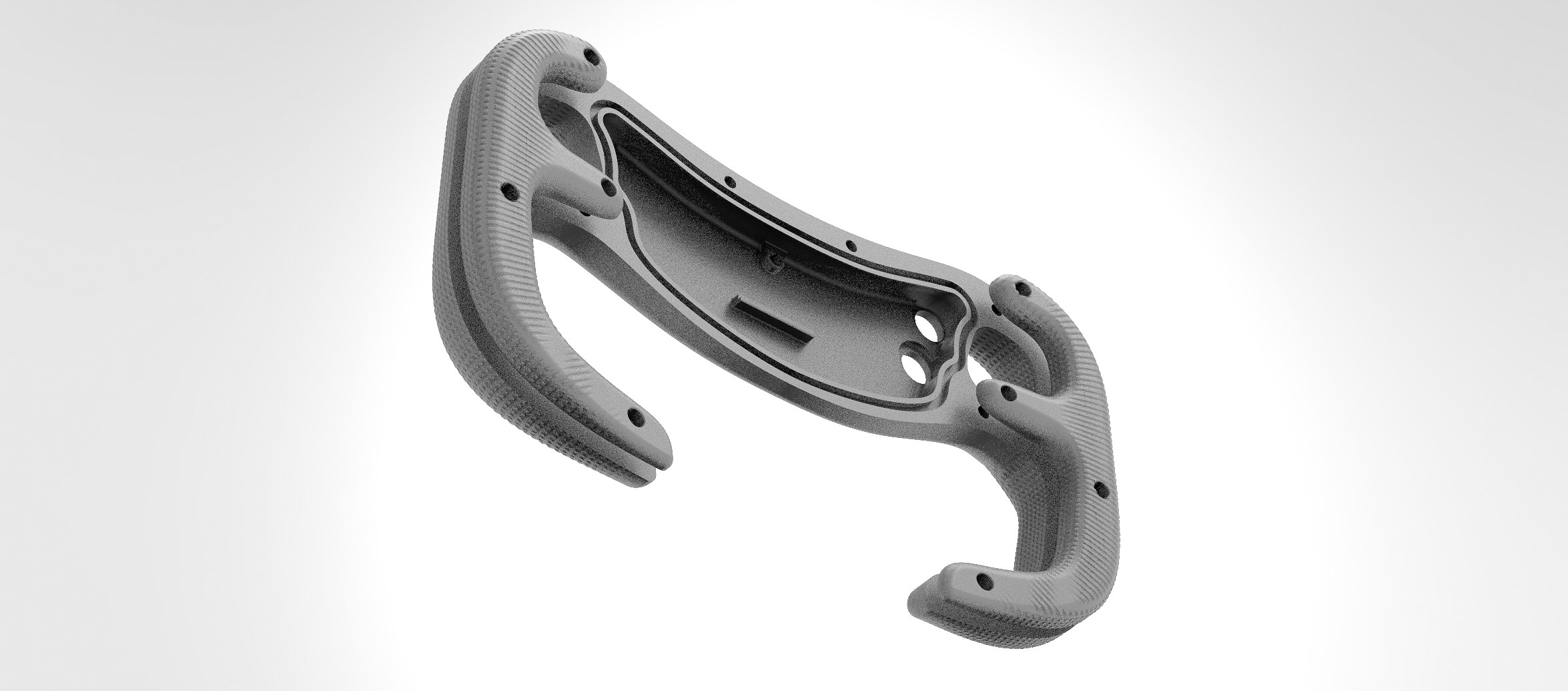
The carbon-fiber mainplate was made in-house!
I waterjet-cut a solid carbon hardpoint placed at the center of Nomex core.
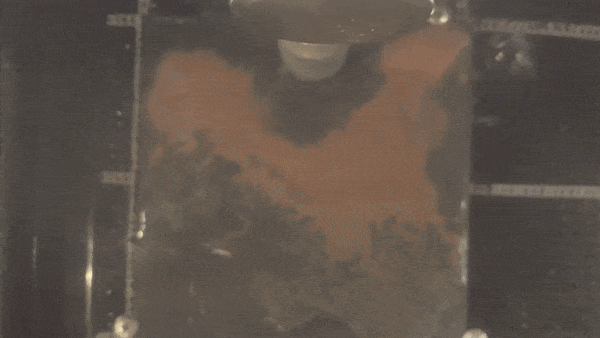
The wet layup of the steering wheel and dashboard plates! Our schedule consisted of 3 plys, core in the middle, and 3 more plys of 200gsm carbon.
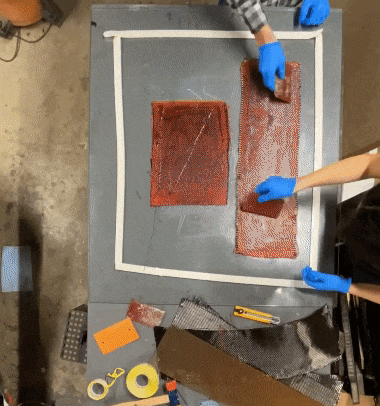
The hardpoint and mainplate silhouettes were waterjet-cut, heat set inserts melted into place, the o-ring secured, wires threaded through cutouts, and the regenerative braking paddles and quick-disconnect were sealed watertight with RTV.

Driver Systems Captain
I led the Driver Systems subteam and managed the development of all the cockpit, and driver touchpoint related projects. I established driver ergonomic criteria, prioritizing safety, accessibility, and comfort while balancing integration, timeline and budget constraints.
Additionally, I conducted project meetings, presented weekly progress checks, onboarded new memebers and worked with other subteam captains to ensure design, timeline, cost and progress of the car was on-track and rules compliant at a higher level.
Additionally, I conducted project meetings, presented weekly progress checks, onboarded new memebers and worked with other subteam captains to ensure design, timeline, cost and progress of the car was on-track and rules compliant at a higher level.


Acceleration and brake pedal
With the switch to our first carbon-fiber monocoque chassis, we reimagined the pedal architecture and mounting. Previously, we used aluminum baseplates for adjustability, but this year we introduced a dovetail rail and bracket system with a detent pin and cam clamp mechanism. This reduced adjustment time from 2 minutes to under 30 seconds and decreased mass by 13.5%.
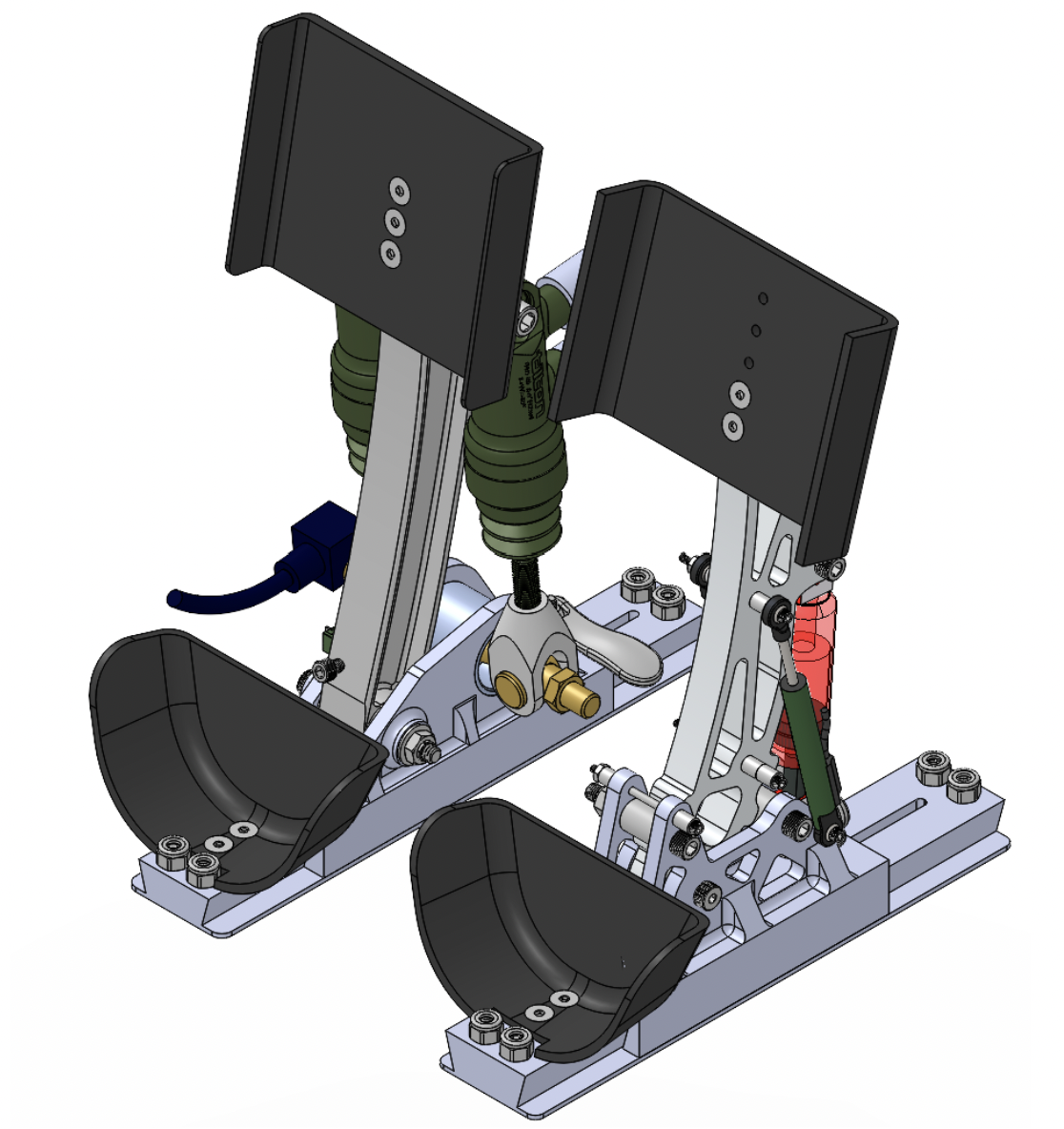

Ergonomic studies helped determine the ideal foot position, brake pedal stiffness, and adjustment distances for drivers of all sizes. All aluminum components, including faceplates and heel cups, were machined in-house.
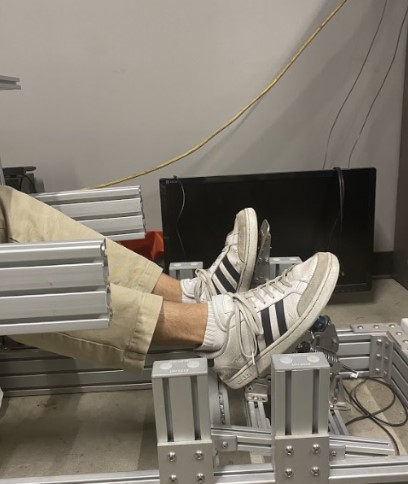


Seat
We developed the team's first single-piece Kevlar-carbon infused seat with double-curved surfaces through a two-year experimental process. To practice for our monocoque chassis manufacturing, we created a machined foam mold and a fiberglass plug, first using a wet layup and later refining the process with resin infusion.
The seat has two front-side mounting points, allowing it to rotate for easy access to the accumulator during charging, eliminating the need to fully remove and realign the seat each time.
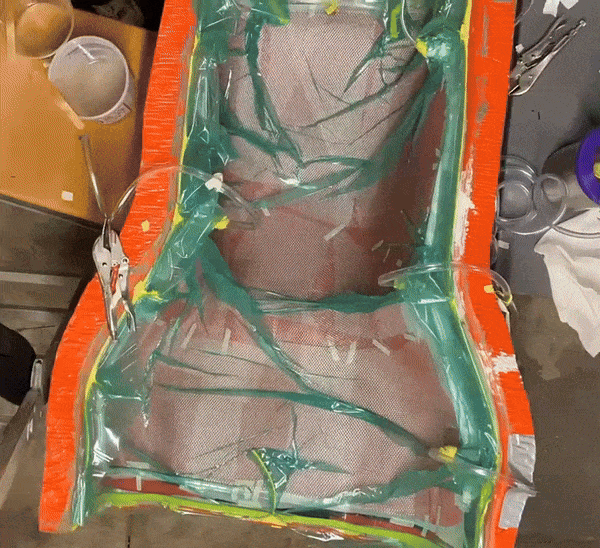

Machining the mold in foam.
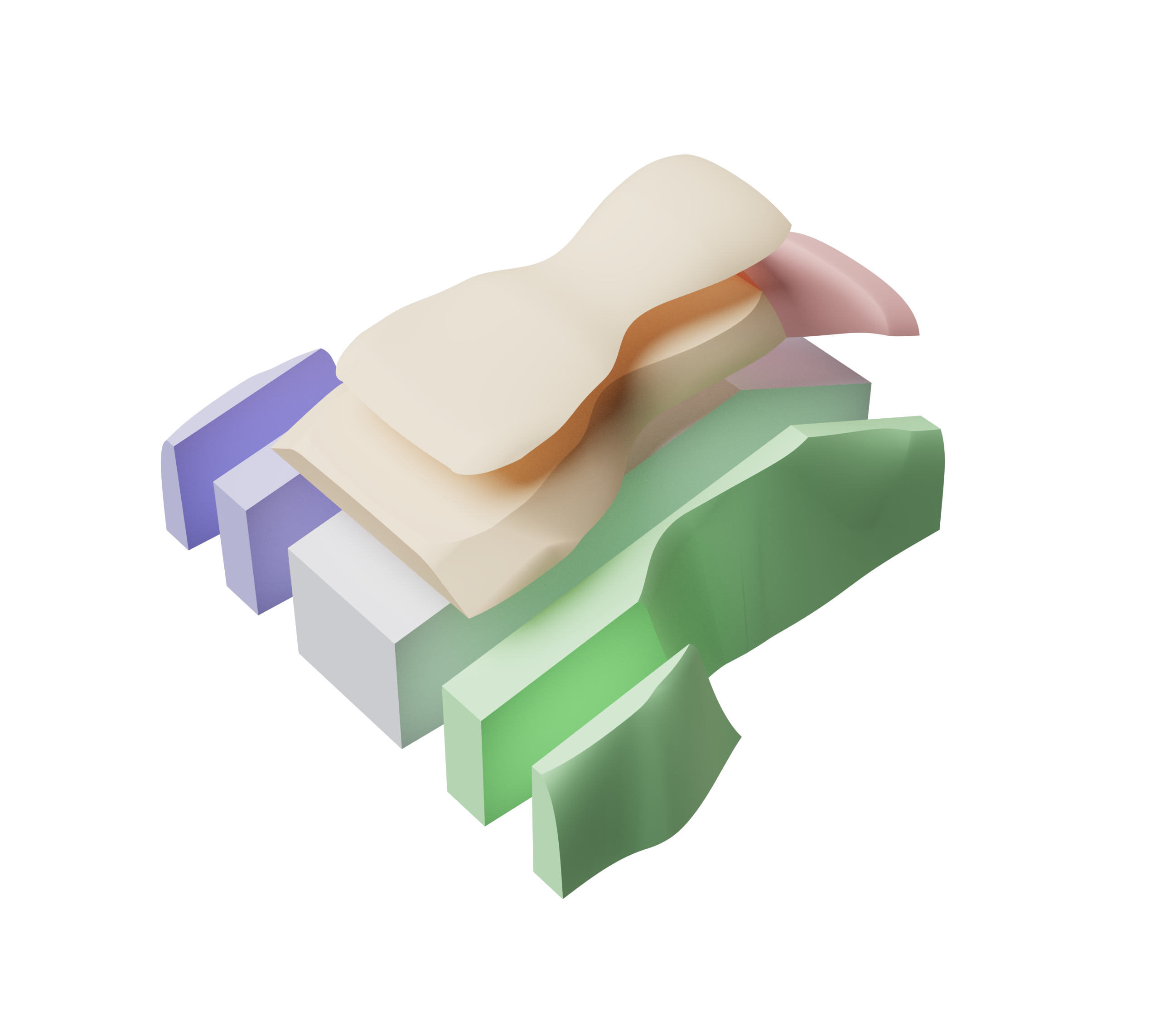
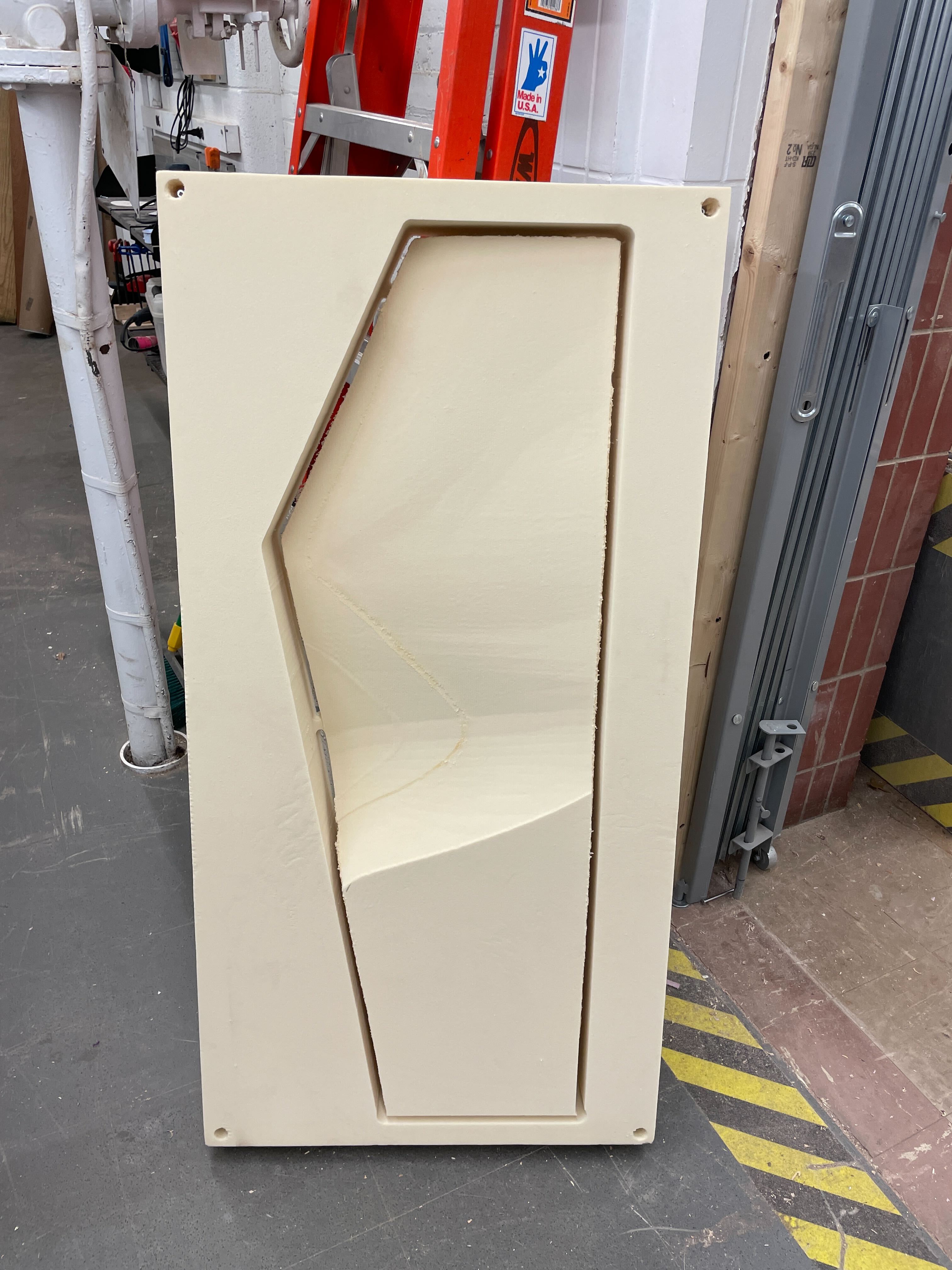
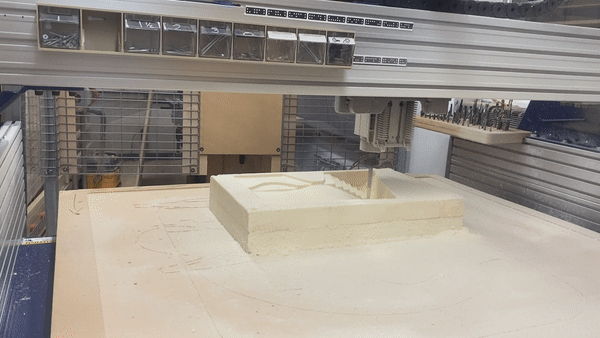
Surface prepping with bondo and primer, and making a plug in gel coat reinforced with fiberglass.
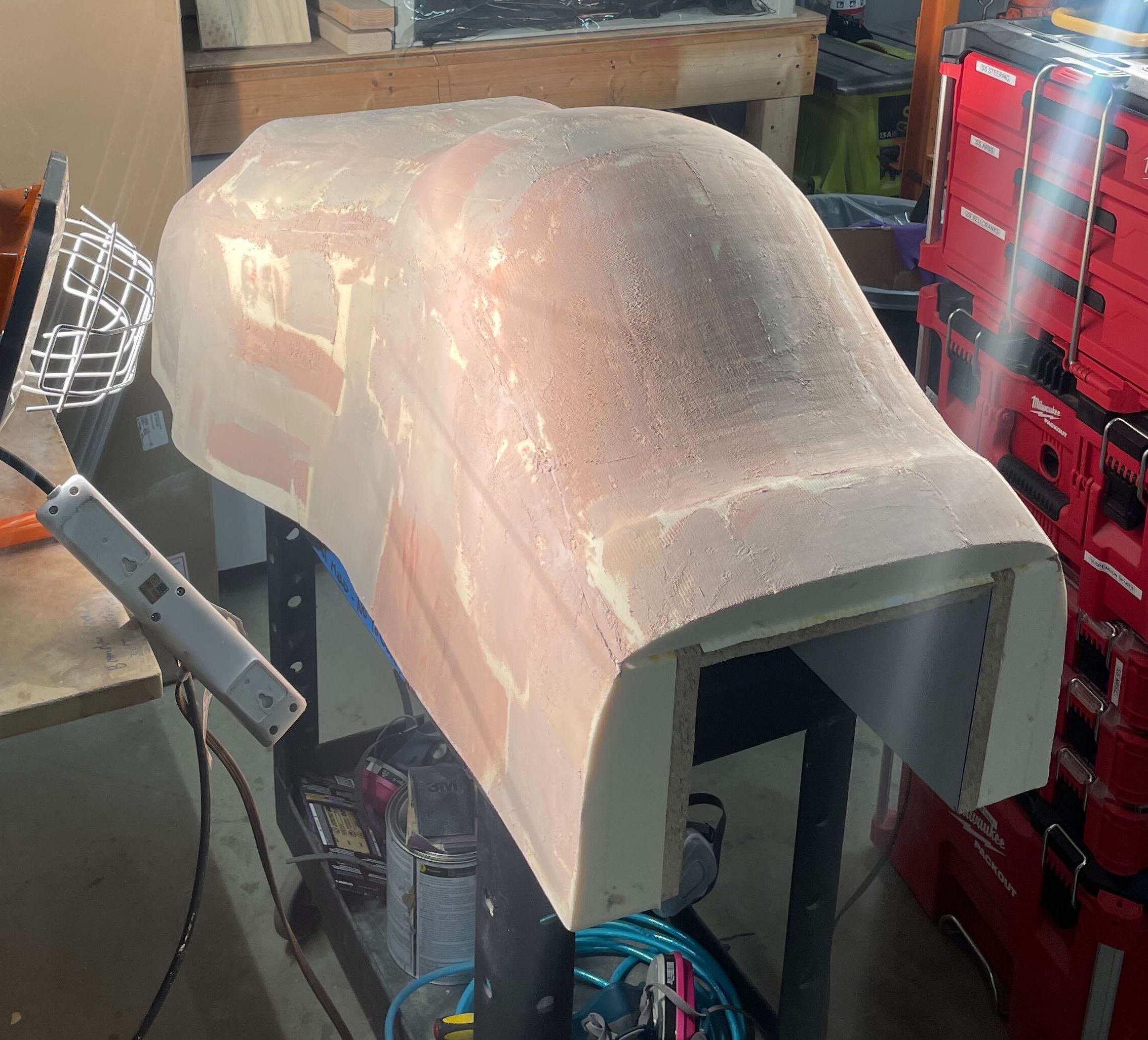
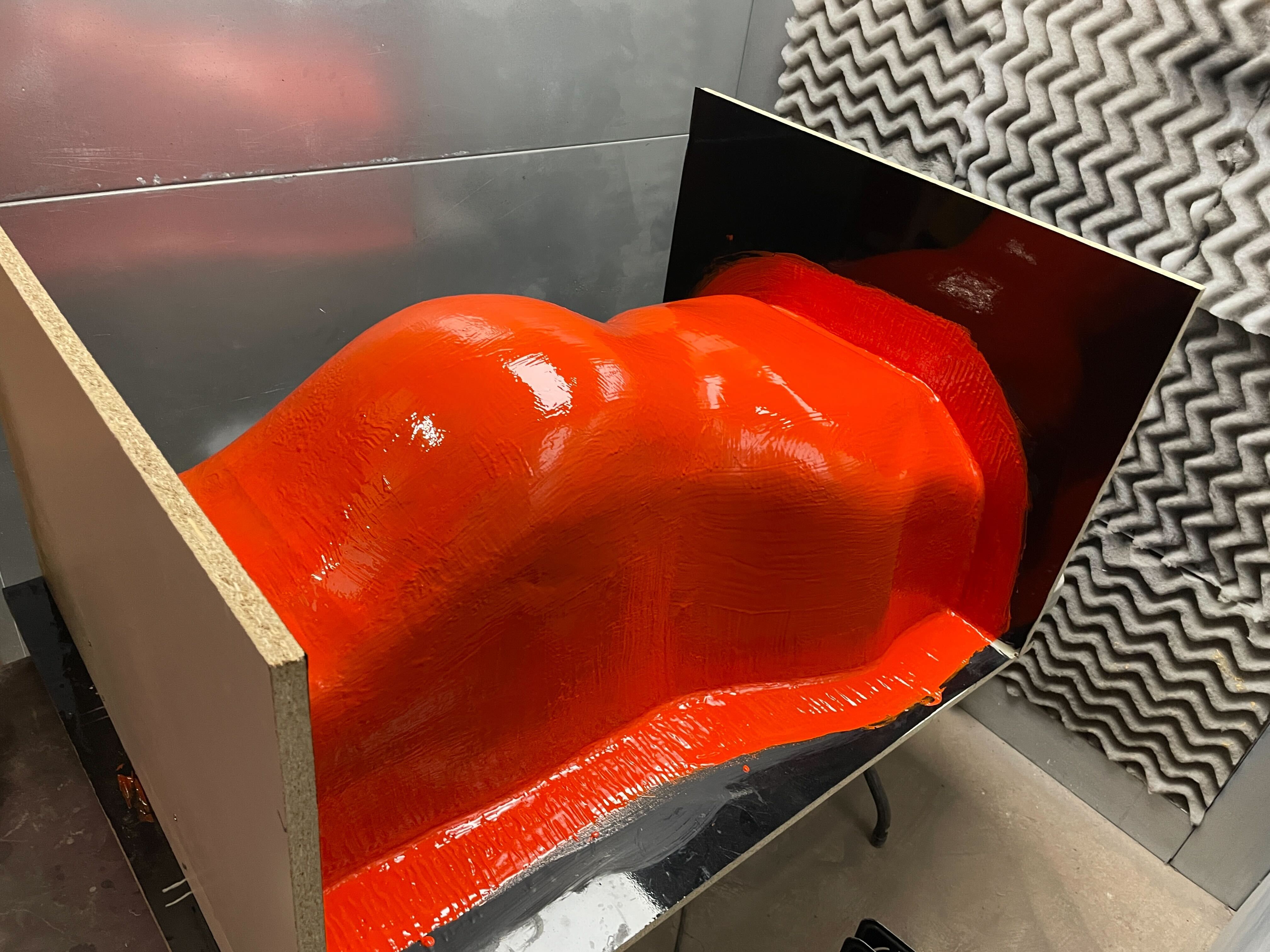
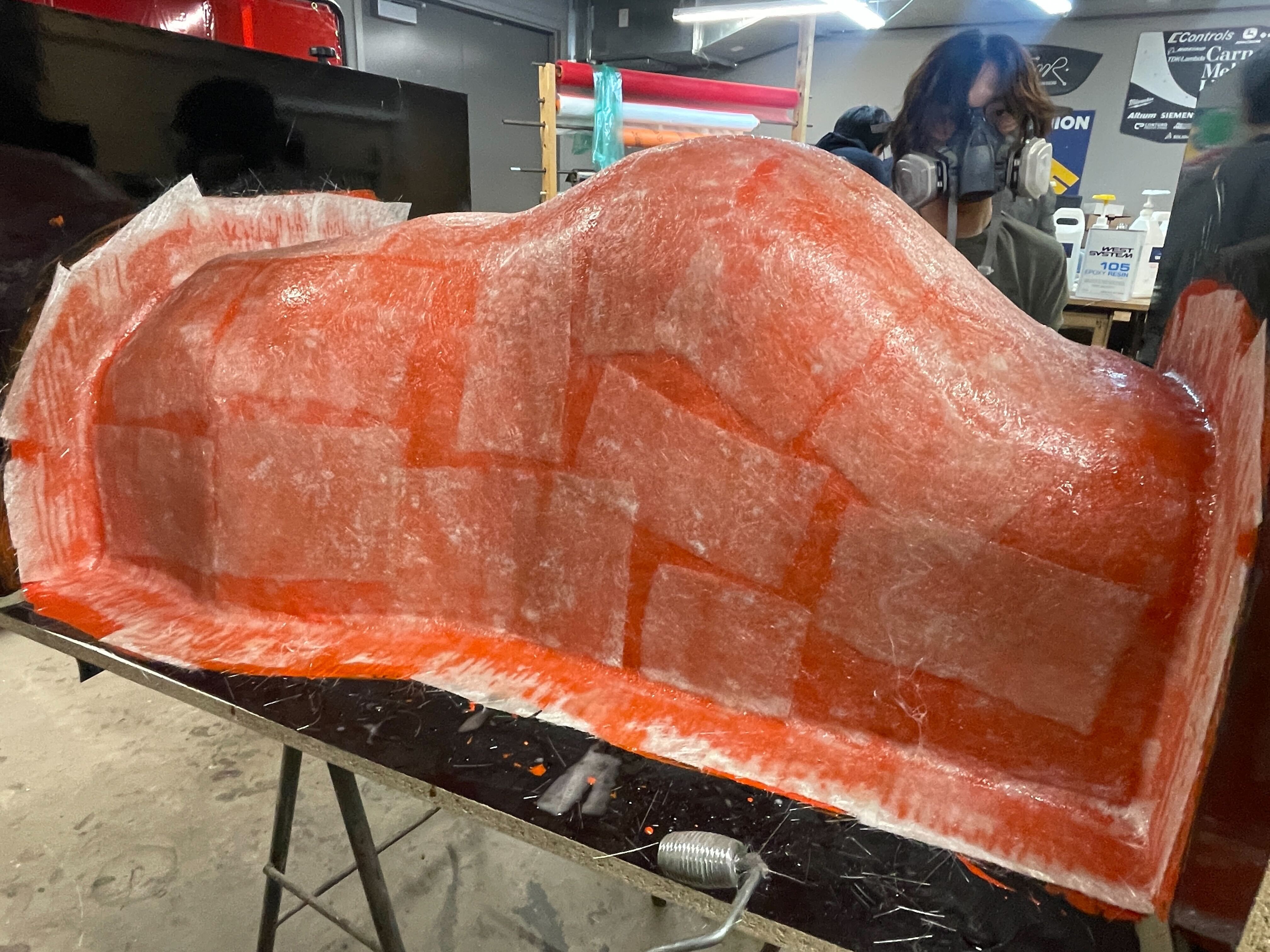
Vaccum infusion process.
Firewall

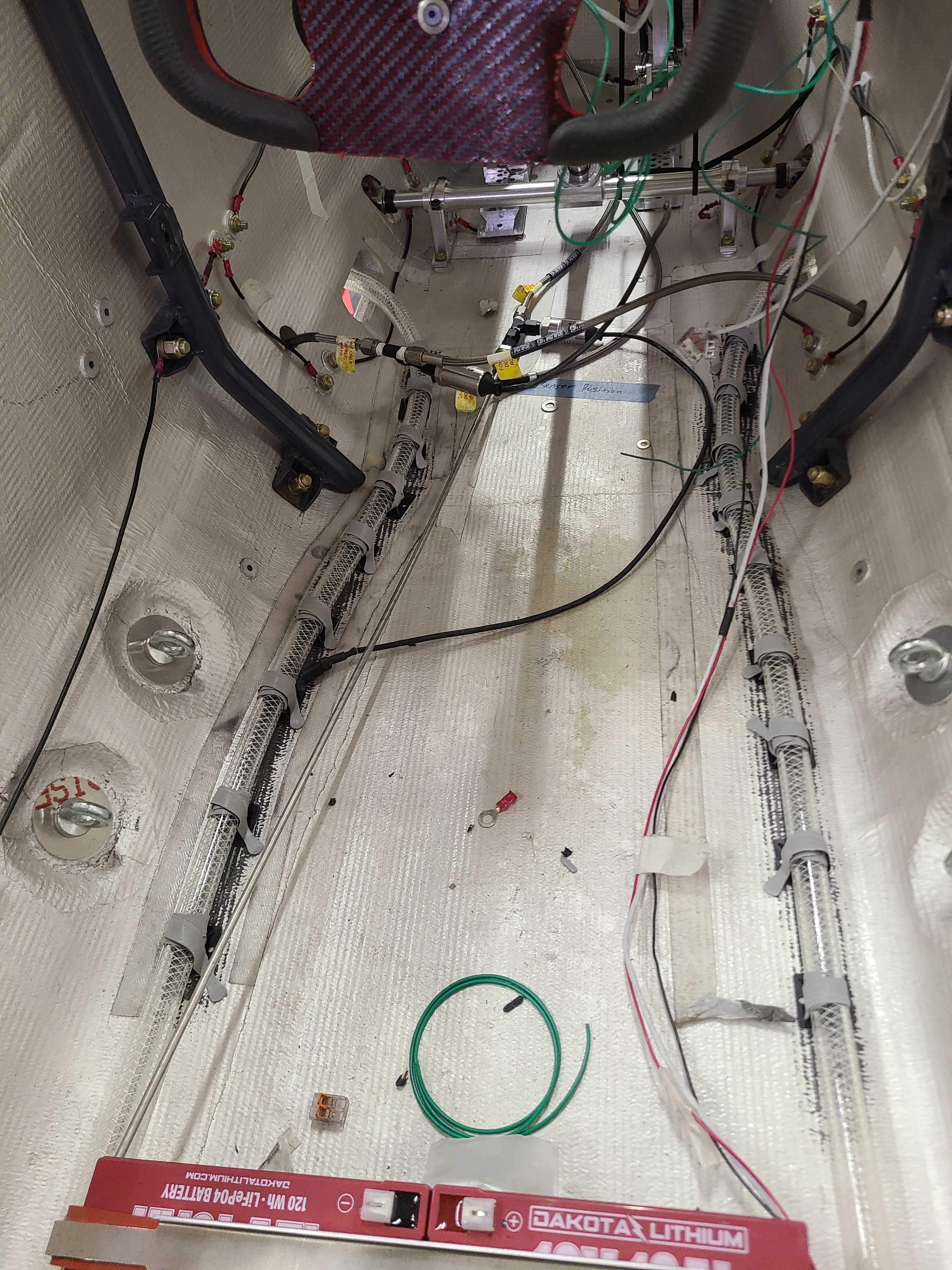
Nosecone



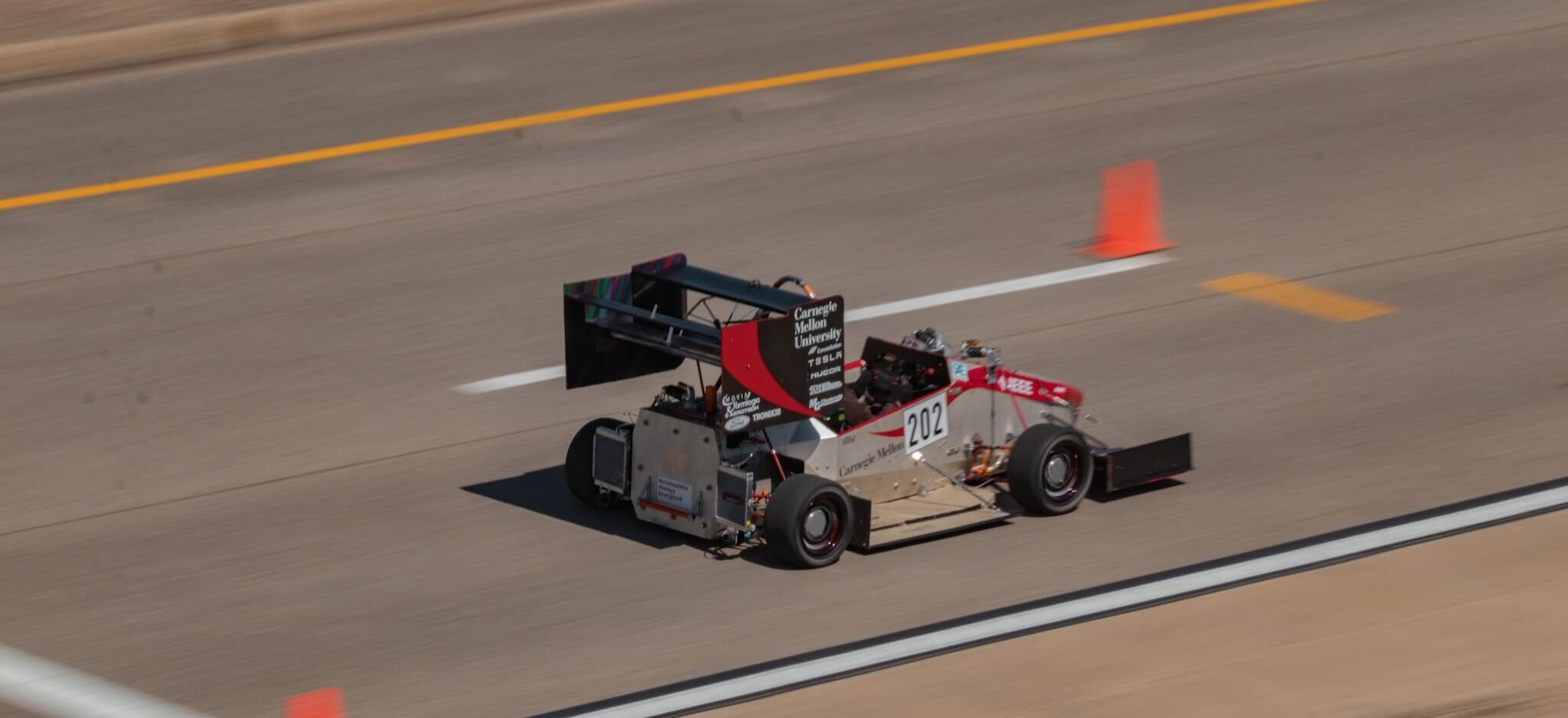
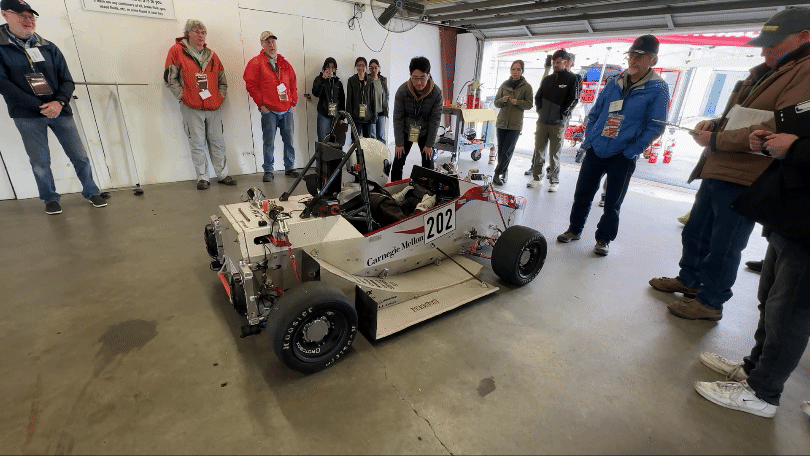
Thanks for visiting <3